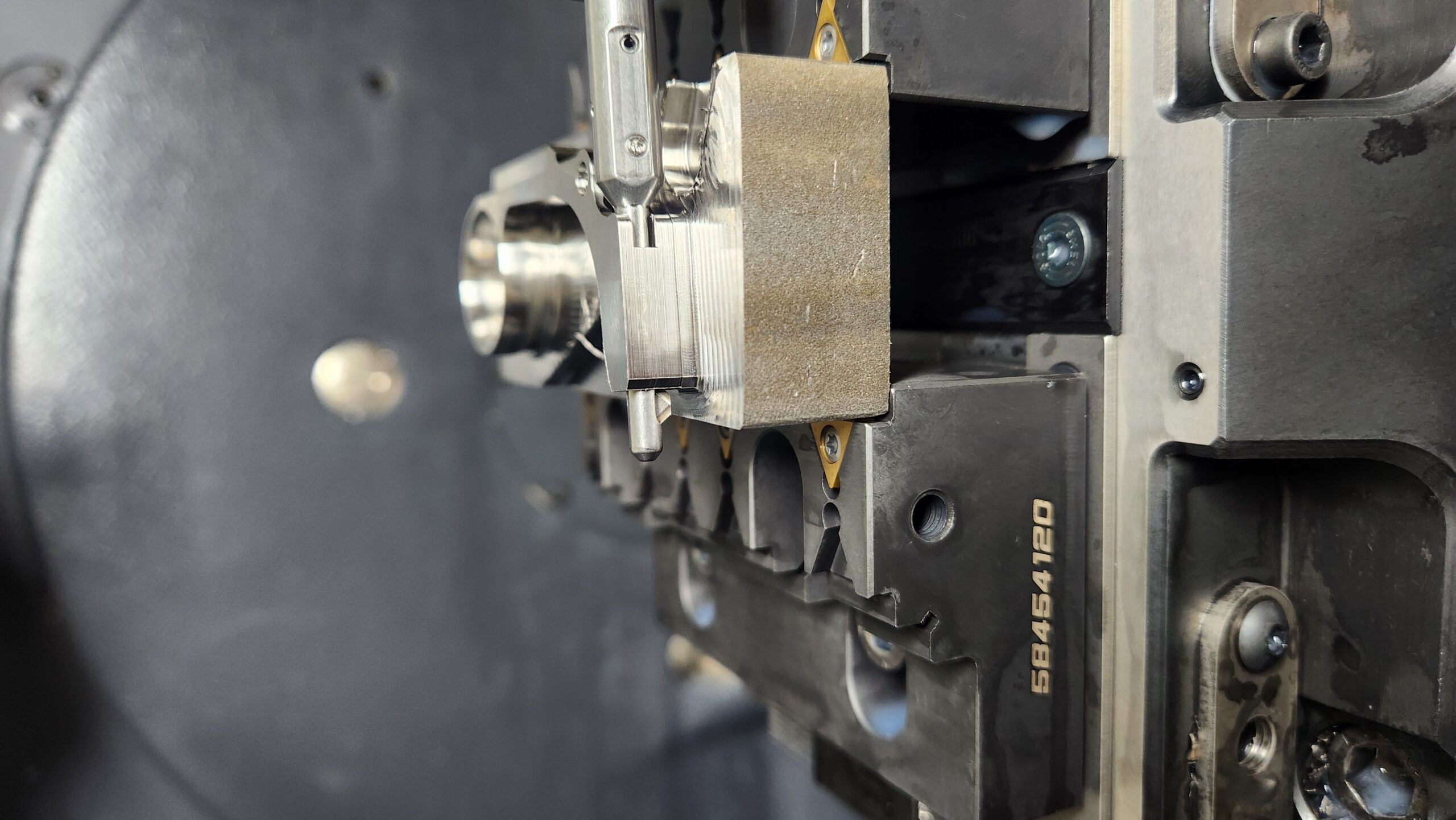
How does the UBURR work?
- Upon insertion, the replaceable and adjustable cutting blade is initially held in the extended position by spring tension, effectively eliminating the burr on the front side of the hole.
- As the cutting tool encounters increased feed pressure, surpassing the preset spring tension, the blade automatically retracts while passing through the pilot-hole. The unique geometry of the blade ensures no marring occurs on the inner surface of the pilot-hole.
- Upon exiting the pilot-hole, spring tension once again triggers the blade to extend, effectively removing the burr on the back side of the hole during the return stroke.

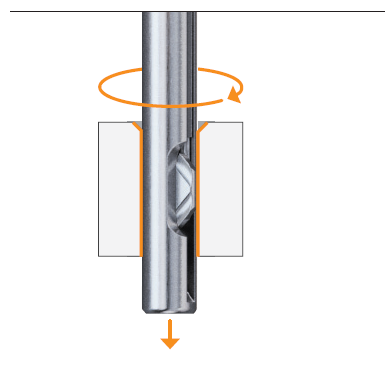
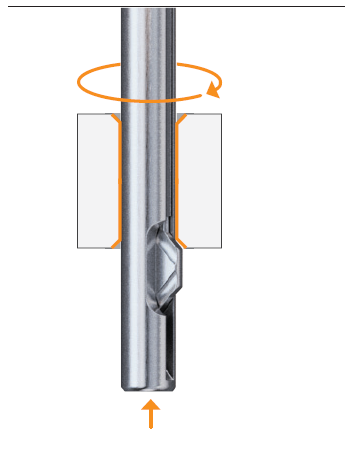
UBURR blade recommendations
UBURR cutting recommendations
The table below presents cutting recommendations, outlining initial feed rates and cutting speed for materials group based on ISO 513 and VDI 3323 standards.
(1) To ensure optimal performance and tool-life under varying conditions:
- For moderate tool-holder or workpiece stability, consider reducing feed rates by up to 10%.
- For poor tool-holder or workpiece stability, it’s advisable to decrease feed rates by up to 30%.
Additionally, the operator must ensure the utilization of appropriate coolant media directed to the cutting tip of the blade and right-hand machining (clockwise).
| HSS Blade | Carbide Blade | HSS or Carbide |
| ||||||||
ISO | Material | Condition | As is | vc cutting speed (1) | vc cutting speed (1) | ƒr cutting feed(1) | Recommended Chip-former | Coolant | ||||
AISI / SAE / ASTM | DIN W.-Nr. | Uncoated m/min. sfm | Coated m/min. sfm | Coated m/min. sfm | Coated/Uncoated mm/rev ipr | |||||||
P | Non-alloy steel and cast steel, free cutting steel | <0.25% C | Annealed | 1020 | 1.0044 | 25-45 80-150 | 45-65 100-165 | 60-120 200-390 | 0.08-0.20 0.003-0.008 | ![]() ![]() | Air / Wet | |
≥0.25% C | Annealed | 1035 | 1.0501 | |||||||||
<0.55% C | Quenched and tempered | 1045 | 1.1201 | |||||||||
≥0.55% C | Annealed | 1055 | 1.0535 | |||||||||
Quenched and tempered | 1060 | 1.1221 | ||||||||||
Low alloy and cast steel (less than 5% of alloying elements) | Annealed | G92600 | 1.5028 | 20-45 80-150 | 35-65 115-165 | 50-120 165-390 | 0.08-0.20 0.003-0.008 | |||||
Quenched and tempered | 4130 | 1.7218 | ||||||||||
4142 | 1.2332 | |||||||||||
5045 | 1.7006 | 20-40 65-130 | 35-55 115-180 | 50-100 165-330 | ||||||||
High alloyed steel, cast steel and tool steel | Annealed | H13 | 1.2344 | 15-35 50-115 | 30-50 100-165 | 45-90 150-295 | 0.08-0.15 0.003-0.006 | |||||
Quenched and tempered | M33 | 1.3249 | ||||||||||
Stainless steel and cast steel | Ferritic/martensitic | 420 | 1.4021 | |||||||||
Martensitic | ||||||||||||
M | Stainless steel | Austenitic, duplex | 304L | 1.4306 | 15-30 50-100 | 30-55 100-180 | 50-100 165-330 | 0.08-0.15 0.003-0.006 | ![]() | Wet | ||
K | Gray cast iron (GG) | Ferritic / pearlitic | Class 25 | 0.6015 | 20-35 65-115 | 35-55 115-180 | 60-120 200-395 | 0.08-0.25 0.003-0.012 | ![]() | Air / Wet | ||
Pearlitic / martensitic | Grade H20 | 036037 | ||||||||||
Nodular cast iron (GGG) | Ferritic | 60-40-18 | 0.7043 | 30-70 100-230 | 40-90 130-295 | 50-100 165-330 | 0.08-0.20 0.005-0.008 | |||||
Pearlitic | F33500 | 0.7050 | ||||||||||
Malleable cast iron | Ferritic | A47 | 0.8135 | |||||||||
Pearlitic | A220 Class | 0.8155 | ||||||||||
N | Aluminum-wrought alloys | Not hardenable | 5005 | 3.3315 | 50-70 165-230 | 75-120 245-395 | 100-160 330-525 | 0.10-0.30 0.004-0.012 | Wet | |||
Hardenable | 7075 | 3.4365 | ||||||||||
Aluminum-cast alloys | ≤12% Si | Not hardenable | 518.0 | 3.3292 | ||||||||
Hardenable | 515.0 | 3.3241 | ||||||||||
>12% Si | High temperature | 390 |
| |||||||||
Copper alloys | >1% Pb | Free cutting | C36000 | 2.0375 | 30-60 100-200 | 45-100 150-330 | 90-130 295-425 | |||||
| Brass | C22000 | 2.0230 | |||||||||
Electrolytic copper | C63000 | 2.0966 | ||||||||||
Non metallic | Duroplastics, fiber plastics | Bakelite |
| 60-100 195-330 | 90-150 295-490 | 180-305 600-1000 | ||||||
Hard rubber | Ebonite |
| ||||||||||
S | High temperature alloys | Fe based | Annealed | 330 | 1.4864 | 10-15 33-50 | 15-35 50-115 | 40-80 130-260 | 0.10-0.20 0.005-0.008 | ![]() |
Wet | |
Hardened | S590 | 1.4977 | ||||||||||
Ni or Co based | Annealed | Incoloy 825 | 2.4858 | Not recommended | 10-15 33-50 | 25-40 80-130 | ||||||
Hardened | Inconel 718 | 2.4668 | ||||||||||
Cast | Nimocast K24 | 2.4674 | ||||||||||
Titanium alloys | Pure | Titanium G.1 | 3.7024 | 10-15 33-50 | 15-20 50-65 | 30-60 100-180 | ||||||
Alpha+beta alloys, hardened | Titanium G.5 | 3.7165 | ||||||||||
H | Hardened steel | Hardened | HARDOX 500 |
| Not recommended | 10-20 10-20 30-65 | 30-50 100-165 |
0.04-0.06 0.0015-0.0024 | Air | |||
Hardened | HARDOX Extreme |
| 10-15 30-50 | 30-40 100-130 | ||||||||
Chilled cast iron | Cast | A532 lllA 25% Cr | 0.9650 | 15-20 50-65 | 45-50 145-165 | |||||||
Cast iron | Hardened | A532 IID 20% CrMo | 0.9645 | 10-20 30-65 | 30-50 100-165 | |||||||
C | Carbon Fiber reinforced plastics (CFRP) | Cured |
– | Not recommended | 90-140 295-460 | 0.05-0.25 0.002-0.010 |
| Air / Wet | ||||
Glass Fiber reinforced plastics (GFRP) | 90-350 295-1150 |
(1) To ensure optimal performance and tool-life under varying conditions:
- For moderate tool-holder or workpiece stability, consider reducing feed rates by up to 10%.
- For poor tool-holder or workpiece stability, it’s advisable to decrease feed rates by up to 30%.
Machining guidelines
- Tool Rotation and Coolant: The UBURR family of tools is suitable for right-hand machining with clockwise tool rotation and should be used with external coolant to flush away chips and swarf from the cutting zone, as shown in Figure 1.
- Geometrical Limitations for Inclined and Cylindrical Surfaces:
- For inclined surfaces (Figure 2), the maximum inclination angle depends on the pilot-hole diameter and can be calculated using the following formula:
- For tubes (Figure 3), it is necessary to ensure that the tool diameter is suitable for the application. This can be verified using the following formula:
- When machining on sloped or cylindrical surfaces, an uneven chamfer will naturally form as illustrated in the accompanying images:
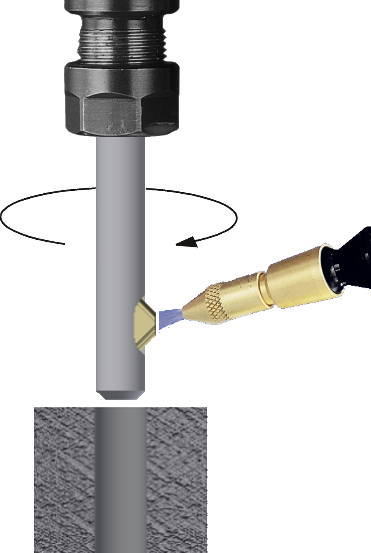
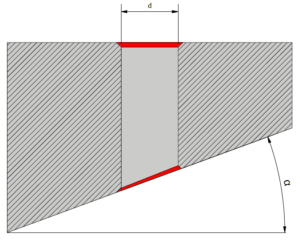
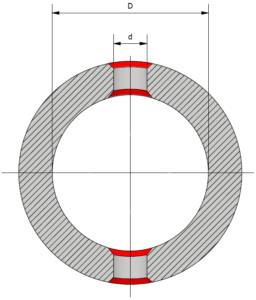
Using the UBURR with electric hand drills:
UBURR is compatible with both CNC machines and electric hand drills, making it suitable for various operational setups and maximizing the manufacturing process.
Programming guidelines
Performing front and back deburring
You can utilize our parametric post routine for milling machines or turning machines to be inserted after each drilling operation:
#101-TOOL LOCATION START
#102-S-CUTTING SPEED, ACCORDING TO CUTTING RECOMMENDATIONS
#103-H1-PILOT HOLE LENGTH
#104-LTB1, ACCORDING TO ITEM TABLE LIST
#105-LTB2, ACCORDING TO ITEM TABLE LIST
#106-RAPID LINEAR FEED FOR POSITION THE TOOL
#107-WORKING CYCLE FEED, ACCORDING TO CUTTING RECOMMENDATIONS
Performing back deburring:
This case involves a different procedure when front deburring is unnecessary.
In such cases, the tool-holder enters the hole without rotating and begins the linear feed only after passing through the pilot hole. Once the tool has passed through the pilot hole, it retracts to execute the back deburring operation:
For performing back deburring, you can also utilize our parametric post for milling machines or turning machines to be inserted after each drilling operation with the same parameters:
#101-TOOL LOCATION START
#102-S-CUTTING SPEED, ACCORDING TO CUTTING RECOMMENDATIONS
#103-H1-PILOT HOLE LENGTH
#105-LTB2, ACCORDING TO ITEM TABLE LIST
#106-RAPID LINEAR FEED FOR POSITION THE TOOL
#107-WORKING CYCLE FEED, ACCORDING TO CUTTING RECOMMENDATIONS
Performing Deburring by Interpolation
UBURR can perform deburring through interpolation, which not only saves on extra tooling costs but also streamlines the production process by integrating multiple functions into one tool.
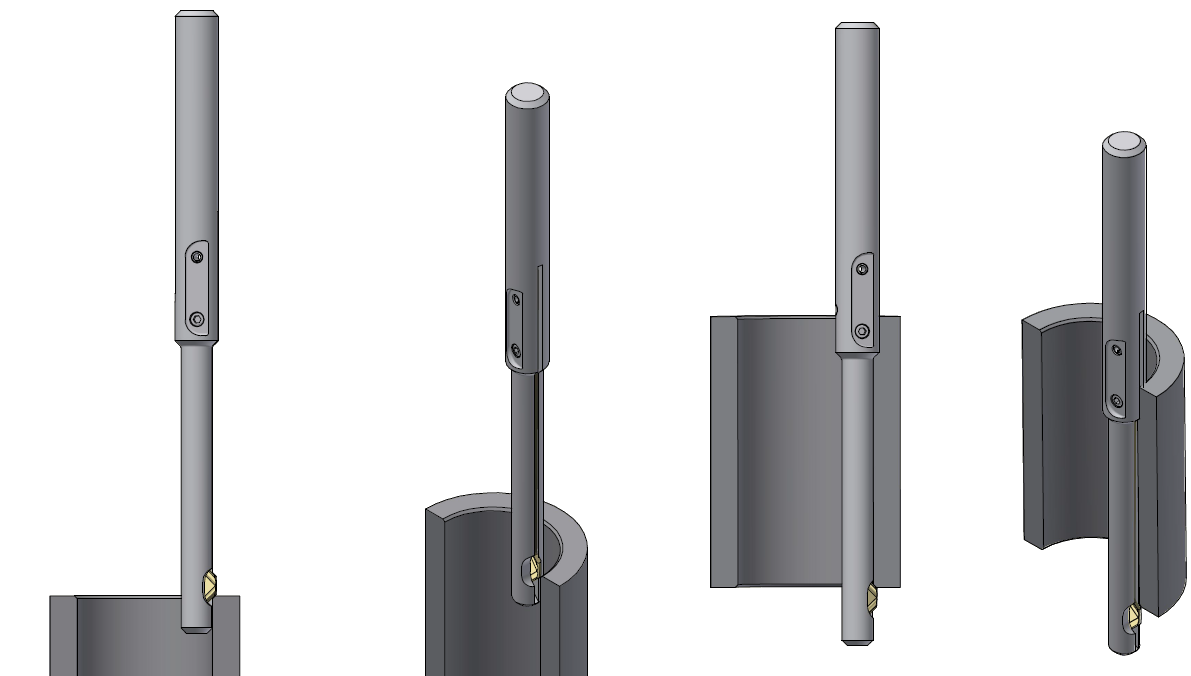
Controlling the chamfer size on the workpiece pilot hole
- The chamfer achieved typically ranges between 0.2mm to 0.5mm (0.008 inches to 0.020 inches).
- The main factor influences the size of the chamfer is the tool selection and the feed.
- If the pilot hole diameter is closer to the minimum recommended pilot hole diameter of the tool (as shown in the item list table) the chamfer size is bigger and Vise-versa.
- For instance, using the UBS-d060-C08-H53-L115 tool (SKU UB3006) and a pilot hole with a diameter of Ø6.0mm (.236”) will yield a larger chamfer compared to a pilot hole with a diameter of Ø6.5mm (0.256”).
- Another option to control the chanfer size is by adjusting the feed rate. Increasing the feed rate (Vf) will decrease the chamfer size, and vice versa.
