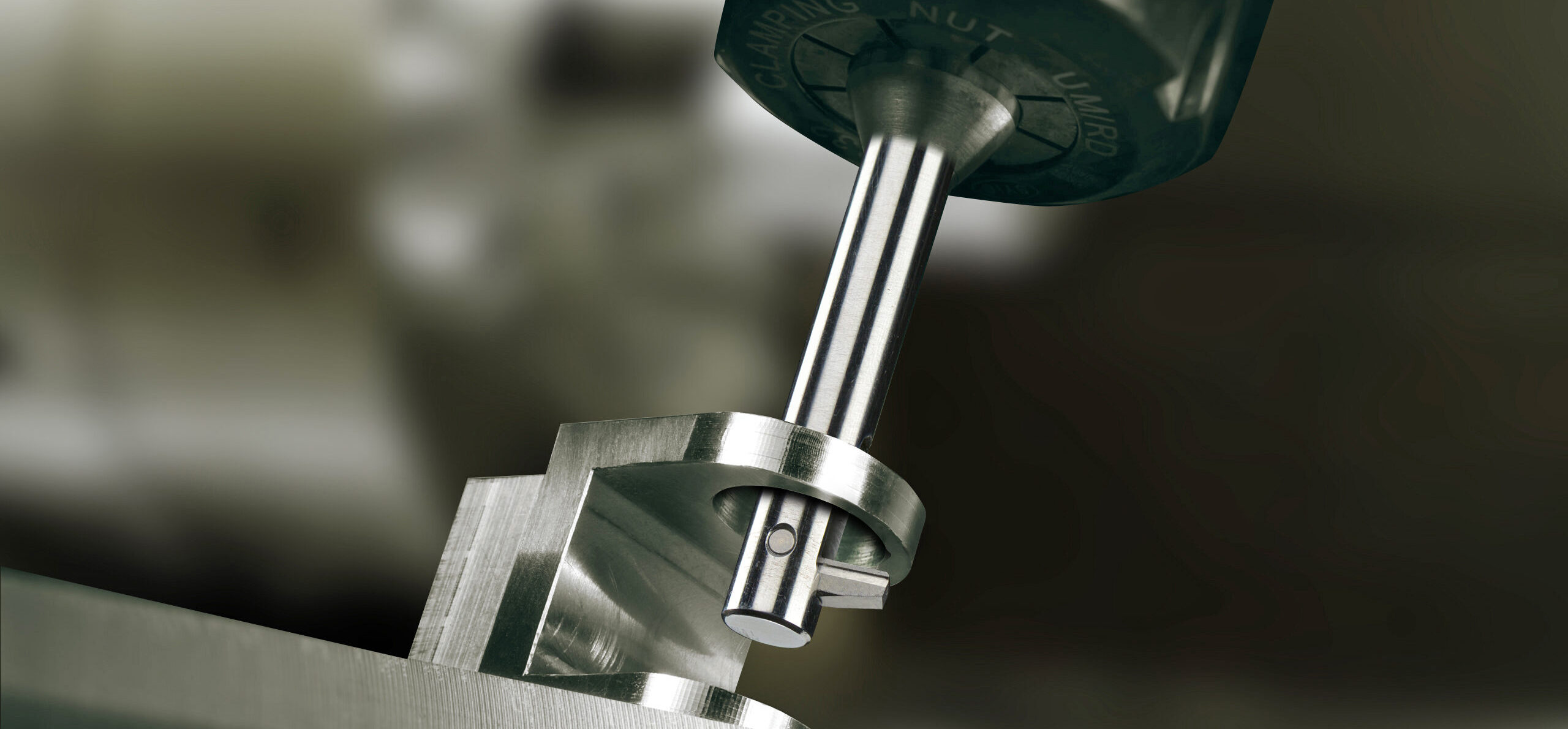
UBACK AND USPOT INSERTS
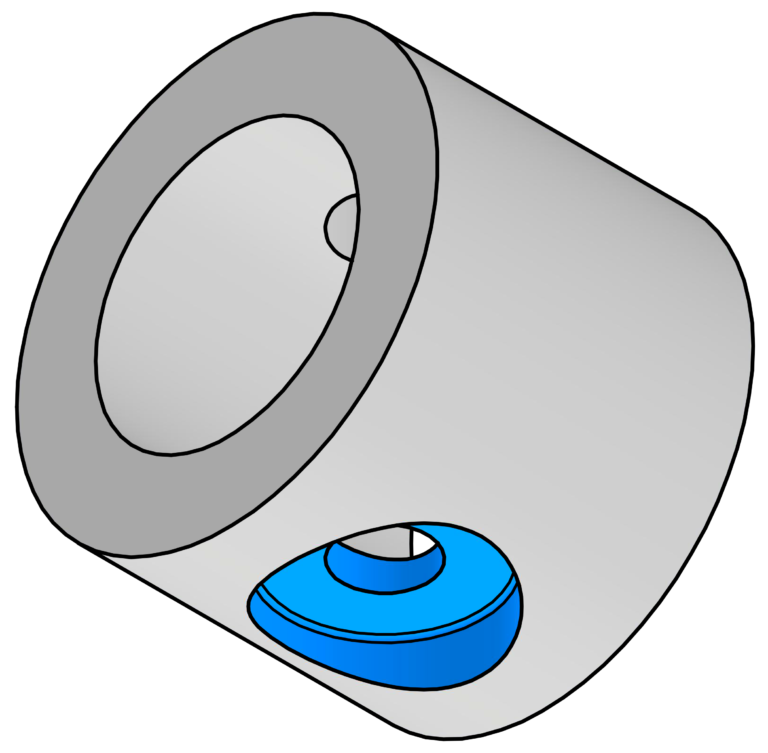
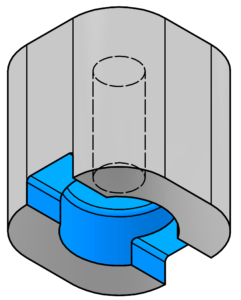
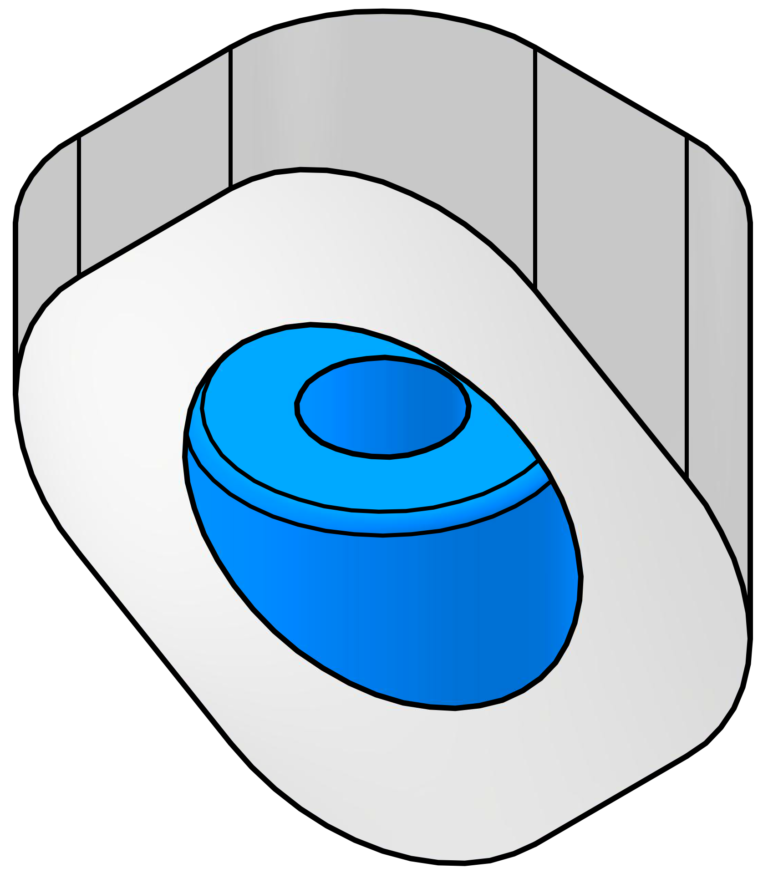
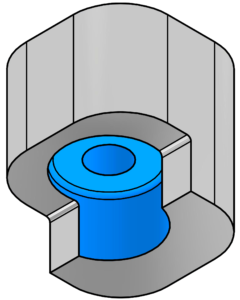
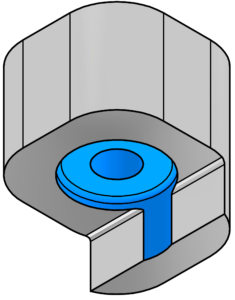
Ultimate Back: Precision Back Counter Solutions
The Ultimate Back line brings together the innovative UX tool-holders and USPOT/UCHAMF inserts to redefine machining precision. Featuring a patented hydraulic mechanism that ingeniously uses the machine’s coolant liquid, this system delivers exceptional control over insert movement. The result? Unparalleled accuracy, repeatability, and streamlined operations for back counterboring, back countersinking, and back spot-facing tasks.
With its advanced engineering, Ultimate Back eliminates the need for workpiece rotation, effortlessly performing operations in a single pass while significantly boosting productivity and efficiency.
Highlights of Ultimate Back
- UX Tool-Holders with Hydraulic Precision: The UX tool-holders feature a hydraulic mechanism powered by coolant pressure, ensuring smooth, accurate, and repeatable insert movement.
- USPOT and UCHAMF Inserts: Designed to handle specific machining needs, these inserts deliver outstanding results in back spot-facing, back counterboring, and back countersinking operations.
- Single-Pass Efficiency: Eliminate workpiece rotation and achieve precise machining in one seamless pass.
- Industry-Grade Reliability: Engineered to meet the rigorous demands of aerospace, automotive, medical, and electronics industries.
- Time and Cost Savings: Reduced cycle times and optimized operations ensure significant productivity gains.
Benefits of Ultimate Back
- Efficient Single Operation: Perform chamfering and counterboring through holes in one pass without rotating the workpiece.
- Customizable Solutions: UX tool-holders support tailored configurations with USPOT and UCHAMF inserts, offering options for coatings, chip-formers, corner radii, and more.
- Innovative Hydraulic Control: UX tool-holders provide precise and consistent operation while simplifying insert replacement.
- Superior Chip Management: Prevent interruptions with excellent chip control for smooth and efficient machining.
- Cost-Effective for All Scales: From small-scale projects to high-volume production, this system delivers exceptional value.
- Automation-Ready Design: Seamlessly integrates into automated manufacturing systems for maximum efficiency.
- Coolant-Driven Mechanism: Operates smoothly with internal coolant, air or emulsion control (minimum 6 bar / 90 PSI), ensuring consistent results.
- Pilot-Hole Protection: The protective insert design safeguards the integrity of the pilot hole during pass-through operations.
- Versatile Applications: UX tool-holders are compatible with a wide range of USPOT and UCHAMF inserts, making them suitable for diverse machining tasks.
- Wide Range of Sizes: The UX tool-holders are available in diameters from Ø8 mm to Ø25 mm (.315-.984”) with various chamfer angles and spotface diameters.
Why Ultimate Back Stands Out
The Ultimate Back system combines the precision of UX tool-holders with the versatility of USPOT and UCHAMF inserts to deliver unparalleled performance. Its innovative design optimizes machining processes, reduces cycle times, and achieves flawless results in high-demand industries.
Whether you’re working in aerospace, automotive, medical, or electronics sectors, Ultimate Back is the ultimate choice for back spot-facing, back counterboring, and back countersinking operations.
What is DURASHIELD?
When you see this logo on our tools, you can trust that you’re holding a product built for excellence. DURASHIELD represents NOGA MT’s premium line of tool-holders, engineered to excel in the most demanding environments. Delivering exceptional performance, extended tool life, and unmatched reliability, DURASHIELD tool-holders feature advanced corrosion resistance and superior structural integrity. They set a new benchmark for strength, durability, and precision, redefining industry standards.
MT DURASHIELD Offering:
Strength: Ensures tools can withstand heavy loads
Toughness: Maintains reliability under demanding conditions
Wear Resistance: Extends tool lifespan and reduces costs
Machinability: Facilitates the design of precise tool-holders
Heat Resistance: Maintains performance at high temperatures
Corrosion Resistance: Ideal for harsh environments
The NOGA MT DURASHIELD family of tool-holders undergoes a passivation process to enhance corrosion resistance. This process eliminates the need for additional coatings and chemicals, simplifies production, reduces environmental impact, and provides a more eco-friendly corrosion protection solution.

UBACK Series and Range with USPOT Inserts for Back Counterbore or Spotface applications:
The UBACK line is organized into series or groups, with each series optimized for a specific pilot-hole range:
Series | Ød Pilot-Hole Range mm /inch | ØDmax. Counterbore Range mm /inch |
B | 8.0–10.0 /0.315–0.394″ | 8.5–23.0 /0.335–0.906″ |
C | 11.0–13.0 /0.433–0.512″ | 11.5–30.0 /0.453–1.181″ |
D | 14.0–16.0 /0.551–0.630″ | 14.5–37.0 /0.571–1.457″ |
E | 17.0–19.0 /0.669–0.748″ | 17.5–44.0 /0.689–1.732″ |
F | 20.0–22.0 /0.787–0.866″ | 20.5–50.5 /0.807–1.988″ |
G | 23.0–25.0 /0.906–0.984″ | 23.5–57.5 /0.925–2.264″ |
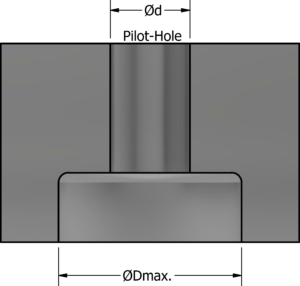
Ødmin. Pilot Hole |
Tool-Holder SKU |
Tool-Holder Description |
ØDS h6 |
FL |
RFC |
H |
L |
L1 |
LTB1(1) |
ØDmax(2) |
Weight (gram) |
Piston Plug(3) |
Insert Clamping Screw M*P*L (mm) |
Series (4) |
8 |
UX2080 |
UX-d080-B-C16-H62-L115 |
16 |
17 |
43 |
62 |
115 |
53 |
6.8 |
18.5 |
69 |
UX0011/ |
UX0005/ M2.5×0.35x7B |
B |
9 |
UX2090 |
UX-d090-B-C16-H62-L115 |
16 |
17.8 |
43 |
62 |
115 |
53 |
6.8 |
21 |
76 |
B |
||
10 |
UX2100 |
UX-d100-B-C16-H62-L115 |
16 |
18.8 |
43 |
62 |
115 |
53 |
6.8 |
23 |
82 |
B |
||
11 |
UX3110 |
UX-d110-C-C16-H80-L133 |
16 |
27 |
52 |
80 |
133 |
53 |
11.4 |
26 |
93 |
UX0011/ |
UX0006/ M3x0.35x10C |
C |
12 |
UX3120 |
UX-d120-C-C16-H80-L133 |
16 |
27.3 |
52 |
80 |
133 |
53 |
11.4 |
28 |
103 |
C |
||
13 |
UX3130 |
UX-d130-C-C16-H80-L133 |
16 |
28 |
52 |
80 |
133 |
53 |
11.4 |
30 |
115 |
C |
||
14 |
UX4140 |
UX-d140-D-C20-H105-L158 |
20 |
32.5 |
72.5 |
105 |
158 |
53 |
13.5 |
32.5 |
160 |
UX0012/ |
UX0007/ M3x0.35x13D |
D |
15 |
UX4150 |
UX-d150-D-C20-H105-L158 |
20 |
32.5 |
72.5 |
105 |
158 |
53 |
13.5 |
34.5 |
178 |
D |
||
16 |
UX4160 |
UX-d160-D-C20-H105-L158 |
20 |
32.5 |
72.5 |
105 |
158 |
53 |
13.5 |
37 |
196 |
D |
||
17 |
UX5170 |
UX-d170-E-C20-H115-L170 |
20 |
38.5 |
76.5 |
115 |
170 |
55 |
16 |
39.5 |
231 |
UX0012/ |
UX0008/ M3x0.35x16E |
E |
18 |
UX5180 |
UX-d180-E-C20-H115-L170 |
20 |
38.5 |
76.5 |
115 |
170 |
55 |
16 |
41.5 |
254 |
E |
||
19 |
UX5190 |
UX-d190-E-C20-H115-L170 |
20 |
38.5 |
76.5 |
115 |
170 |
55 |
16 |
44 |
278 |
E |
||
20 |
UX6200 |
UX-d200-F-C25-H120-L175 |
25 |
43.5 |
76.5 |
120 |
175 |
55 |
17.8 |
46 |
344 |
UX0013/ |
UX0009/ M4x0.5x19F |
F |
21 |
UX6210 |
UX-d210-F-C25-H120-L175 |
25 |
43.5 |
76.5 |
120 |
175 |
55 |
17.8 |
48.5 |
373 |
F |
||
22 |
UX6220 |
UX-d220-F-C25-H120-L175 |
25 |
43.5 |
76.5 |
120 |
175 |
55 |
17.8 |
50.5 |
403 |
F |
||
23 |
UX7230 |
UX-d230-G-C25-H120-L175 |
25 |
48 |
72 |
120 |
175 |
55 |
20 |
53 |
427 |
UX0013/ |
UX0010/ M4x0.5x21G |
G |
24 |
UX7240 |
UX-d240-G-C25-H120-L175 |
25 |
48 |
72 |
120 |
175 |
55 |
20 |
55.5 |
445 |
G |
||
25 |
UX7250 |
UX-d250-G-C25-H120-L175 |
25 |
48 |
72 |
120 |
175 |
55 |
20 |
57.5 |
492 |
G |
(1) The LTB parameter varies between USPOT and UCHAMF inserts.
(2) The achieved tolerance for the counterbore or spotface diameter (ØD) is ±0.1 mm (0.004″)
(3) Piston plug designed to adapt to different coolant systems. For more info, click here.
(4) The insert series must match the series of the tool holder.
Note: Tool-holders and inserts are sold separately.
- UX Tool-holders spare parts:
- SP0105 Hex L-Key 0.050" 1+1/16/1+9/16
- UX0003 Pin for Insert Replacement
- Insert Clamping Screw – according to the table above
- UX0011 M5 x 6 mm plug set screw
Ødmin. Pilot Hole |
Tool-Holder SKU |
Tool-Holder Description |
ØDS h6 |
FL |
RFC |
H |
L |
L1 |
LTB1(1) |
ØDmax(2) |
Weight (lbs) |
Piston Plug(3) |
Insert Clamping Screw M*P*L (mm) |
Series (4) |
0.315 |
UX2080 |
UX-d080-B-C16-H62-L115 |
0.630 |
0.669 |
1.693 |
2.441 |
4.528 |
2.087 |
0.268 |
0.728 |
0.1521 |
UX0011/ |
UX0005/ M2.5×0.35x7B |
B |
0.354 |
UX2090 |
UX-d090-B-C16-H62-L115 |
0.630 |
0.701 |
1.693 |
2.441 |
4.528 |
2.087 |
0.268 |
0.827 |
0.1676 |
B |
||
0.394 |
UX2100 |
UX-d100-B-C16-H62-L115 |
0.630 |
0.740 |
1.693 |
2.441 |
4.528 |
2.087 |
0.268 |
0.906 |
0.1808 |
B |
||
0.433 |
UX3110 |
UX-d110-C-C16-H80-L133 |
0.630 |
1.063 |
2.047 |
3.150 |
5.236 |
2.087 |
0.449 |
1.024 |
0.205 |
UX0011/ |
UX0006/ M3x0.35x10C |
C |
0.472 |
UX3120 |
UX-d120-C-C16-H80-L133 |
0.630 |
1.075 |
2.047 |
3.150 |
5.236 |
2.087 |
0.449 |
1.102 |
0.2271 |
C |
||
0.512 |
UX3130 |
UX-d130-C-C16-H80-L133 |
0.630 |
1.102 |
2.047 |
3.150 |
5.236 |
2.087 |
0.449 |
1.181 |
0.2535 |
C |
||
0.551 |
UX4140 |
UX-d140-D-C20-H105-L158 |
0.787 |
1.280 |
2.854 |
4.134 |
6.220 |
2.087 |
0.531 |
1.280 |
0.3527 |
UX0012/ |
UX0007/ M3x0.35x13D |
D |
0.591 |
UX4150 |
UX-d150-D-C20-H105-L158 |
0.787 |
1.280 |
2.854 |
4.134 |
6.220 |
2.087 |
0.531 |
1.358 |
0.3924 |
D |
||
0.630 |
UX4160 |
UX-d160-D-C20-H105-L158 |
0.787 |
1.280 |
2.854 |
4.134 |
6.220 |
2.087 |
0.531 |
1.457 |
0.4321 |
D |
||
0.669 |
UX5170 |
UX-d170-E-C20-H115-L170 |
0.787 |
1.516 |
3.012 |
4.528 |
6.693 |
2.165 |
0.630 |
1.555 |
0.5093 |
UX0012/ |
UX0008/ M3x0.35x16E |
E |
0.709 |
UX5180 |
UX-d180-E-C20-H115-L170 |
0.787 |
1.516 |
3.012 |
4.528 |
6.693 |
2.165 |
0.630 |
1.634 |
0.56 |
E |
||
0.748 |
UX5190 |
UX-d190-E-C20-H115-L170 |
0.787 |
1.516 |
3.012 |
4.528 |
6.693 |
2.165 |
0.630 |
1.732 |
0.6129 |
E |
||
0.787 |
UX6200 |
UX-d200-F-C25-H120-L175 |
0.984 |
1.713 |
3.012 |
4.724 |
6.890 |
2.165 |
0.701 |
1.811 |
0.7584 |
UX0013/ |
UX0009/ M4x0.5x19F |
F |
0.827 |
UX6210 |
UX-d210-F-C25-H120-L175 |
0.984 |
1.713 |
3.012 |
4.724 |
6.890 |
2.165 |
0.701 |
1.909 |
0.8223 |
F |
||
0.866 |
UX6220 |
UX-d220-F-C25-H120-L175 |
0.984 |
1.713 |
3.012 |
4.724 |
6.890 |
2.165 |
0.701 |
1.988 |
0.8885 |
F |
||
0.906 |
UX7230 |
UX-d230-G-C25-H120-L175 |
0.984 |
1.890 |
2.835 |
4.724 |
6.890 |
2.165 |
0.787 |
2.087 |
0.9414 |
UX0013/ |
UX0010/ M4x0.5x21G |
G |
0.945 |
UX7240 |
UX-d240-G-C25-H120-L175 |
0.984 |
1.890 |
2.835 |
4.724 |
6.890 |
2.165 |
0.787 |
2.185 |
0.9811 |
G |
||
0.984 |
UX7250 |
UX-d250-G-C25-H120-L175 |
0.984 |
1.890 |
2.835 |
4.724 |
6.890 |
2.165 |
0.787 |
2.264 |
1.0847 |
G |
(1) The LTB parameter varies between USPOT and UCHAMF inserts.
(2) The achieved tolerance for the counterbore or spotface diameter (ØD) is ±0.1 mm (0.004″)
(3) Piston plug designed to adapt to different coolant systems. For more info, click here.
(4) The insert series must match the series of the tool holder.
Note: Tool-holders and inserts are sold separately.
- UX Tool-holders spare parts:
- SP0105 Hex L-Key 0.050" 1+1/16/1+9/16
- UX0003 Pin for Insert Replacement
- Insert Clamping Screw – according to the table above
- UX0011 M5 x 6 mm plug set screw
UBACK tool-holders coding system specifications and identification:
Ordering special UBack Tool-holders
We can also modify or produce tailor-made tool-holders.
If you need further assistance, please don’t hesitate to contact us.
Providing an application drawing or sketch, the raw material details, and any other relevant information will help us assist you more effectively.
How to Select the Correct Tool-Holder and USPOT Insert to Match Your Application:
The USPOT inserts are available as semi-standard solutions tailored to customer applications.
- Choose the appropriate tool-holder based on the pilot hole diameter.
For instance, if the pilot hole diameter is 8.5 mm, select the UX2080, which supports a minimum diameter (Ødmin) of 8 mm. - Specify the required parameters for the USPOT insert, including the counter-bore or spotface diameter, corner radius, chip-former, and coating.
- Fill in the relevant details for the USPOT insert description as outlined in the specifications below.
- Ensure compatibility between the USPOT insert series and the corresponding UX tool-holder. The series of the insert must match the series of the tool-holder.
Notes:
- Coating – Our top recommendation is the NCT grade, featuring the versatile TiAlN PVD coating. It offers excellent thermal stability, oxidation resistance, and is compatible with a wide range of materials, including mild steels, stainless steel, and Inconel. For additional options, refer to the list of available coatings below.
- Tool-holders and inserts are sold separately.
USPOT inserts coding system specifications and identification:
USPOT- Ordering Special Inserts:
Here is an example of coding a special USPOT insert for the application shown on the right:
Ød = 8.7mm (0.343″)
ØD = 17.6mm (0.693″)
R = 0.2mm (0.032″)
Material: AISI 4340 / 34CrNiMo6 (1.6582) / SNCM439, tempered to 42 HRC
The recommended tool-holder is UX2080 / UX-d080-B-C16-H62-L115
The corresponding insert is US-d087-D176-B-R02-ML-NCT
Important Note:
Ensure that the pilot-hole length (L) is less than or equal to the RFC (Relief For Cutting) L⩽RFC ,as specified in the UBACK tool-holders table below.
If you need further assistance, please don’t hesitate to contact us.
Providing an application drawing or sketch, the raw material specifications, and any other relevant information will help us assist you more effectively.
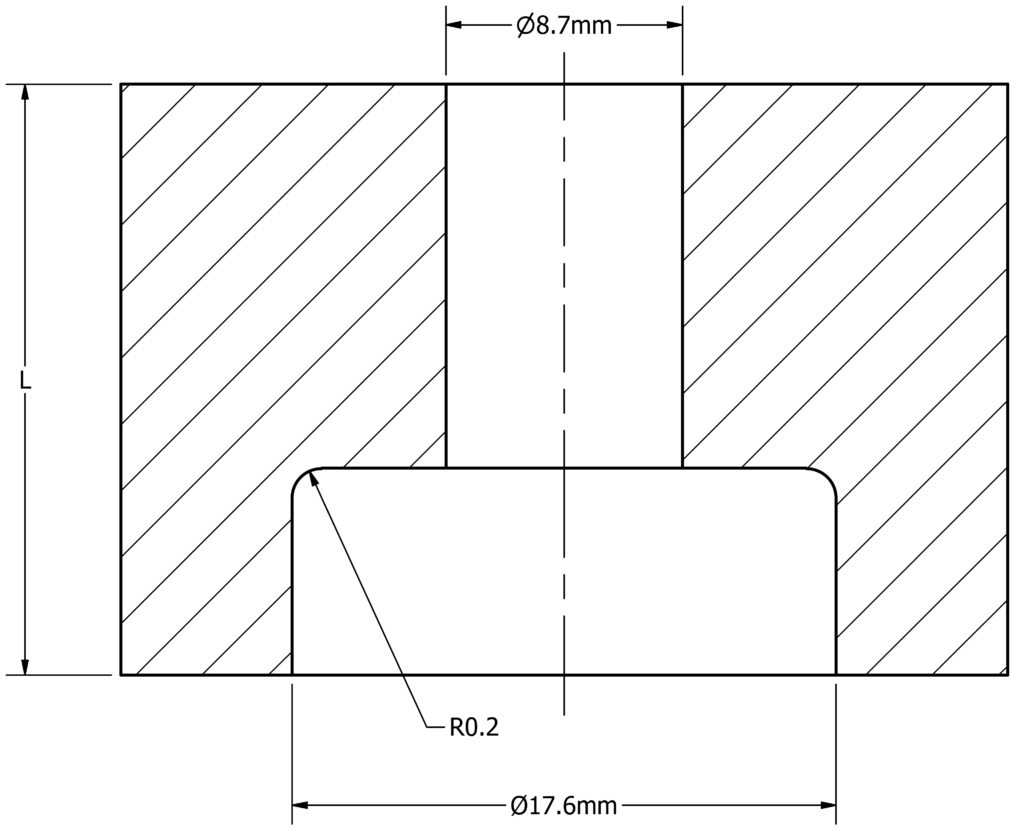
Try Using our USPOT Code Generator & Tool-Holder Helper Below
Available Coating types and surface treatments:
Coating |
Key Features |
Applications |
Industries |
Material Examples |
ISO GROUP |
|||||
P |
M |
K |
N |
S |
H |
|||||
TiAlN |
Suitable for mid steels, cast iron, stainless steel, titanium alloys, Inconel, tool steel, and hardened steels. Offers excellent thermal stability, oxidation resistance, and wear resistance. |
Ideal for high-speed cutting and general-purpose machining. Performs well in both wet and dry conditions. |
Aerospace, Automotive, General Engineering |
AISI 304, 42CrMo4, GG (Grey Cast Iron), Ti6Al4V |
✓ |
✓ |
✓ |
X |
✓ |
✓ |
TiAlSiN |
Provides exceptional hardness and oxidation resis9tance, withstanding temperatures above 1,200°C. Suitable for high-strength steels, superalloys, hardened steels (over 45 Rc), and titanium alloys. |
Best for high-performance machining in demanding environments. Excels in dry machining at high speeds. |
Aerospace, Automotive, Die and Mold |
Inconel 718, AISI 4140, Ti6Al4V |
✓ |
✓ |
X |
X |
✓ |
X |
AlTiSiN |
Offers high hardness, thermal stability, and resistance to wear and oxidation. Suitable for stainless steel, hardened cast, superalloys, and steels over 45 Rc. |
Designed for high-speed machining in extreme conditions. Performs exceptionally in dry machining. |
Aerospace, Automotive, Precision Engineering |
AISI 316, AISI H13, Hastelloy |
X |
✓ |
X |
X |
✓ |
✓ |
AlCrN |
Provides excellent oxidation resistance (up to 1,100°C), toughness, and abrasion resistance. Suitable for carbon steels, cast iron, stainless steel, and aluminum. |
Suitable for general machining in wet and dry environments. Excels in abrasive and high-wear applications. |
Automotive, Aerospace, Die and Mold |
AISI 304, AISI 1045, GG, AL6061 |
✓ |
X |
✓ |
✓ |
X |
X |
AlTiN |
High hardness, wear resistance, and thermal stability up to 1,100°C. Designed for mid steels, cast iron, high-speed steels, tool steel, and hardened materials. |
Ideal for heavy-duty machining and high-speed cutting. Performs well in dry and abrasive conditions. |
Aerospace, Automotive, Heavy Engineering |
AISI 4340, M2 HSS, GG (Grey Cast Iron) |
✓ |
✓ |
✓ |
X |
X |
X |
TiB2 |
Kknown for exceptional chemical stability, low friction, and high thermal conductivity. Best for machining non-ferrous materials such as aluminium, copper, brass, and magnesium alloys. Reduces friction and Built-Up Edge. (BUE) |
Optimized for high-speed machining of non-ferrous metals. Prevents material adhesion and improves efficiency. |
Aerospace, Automotive, Electronics |
AL7075, 6061-T6, Copper, Magnesium Alloys (AZ31) |
X |
X |
X |
✓ |
✓ |
X |
Polishing |
Provides a smooth, refined surface finish by removing micro-defects, scratches, or burrs. Enhances aesthetics and surface quality. Reduces friction and BUE. |
Suitable for machining aluminium with high speeds and high MRR (Metal Removal Rates) |
Aerospace, Automotive |
AL7075, 6061-T6, Copper, Magnesium Alloys (AZ31) |
X |
X |
X |
✓ |
X |
X |
Chip-Formers:
PL
Positive cutting land
Suitable for all around purpose
and ISO P,M,K,N,S
as well as composite materials
ML
Moderate cutting land
Suitable for and ISO P,M,K,S,H
Materials
HL
Negative cutting land
Suitable for and ISO P,M,K,S,H
Materials
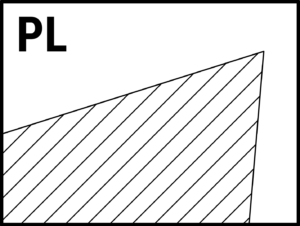
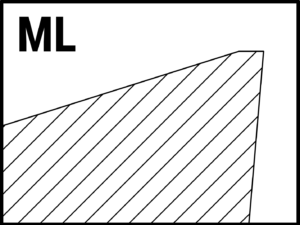
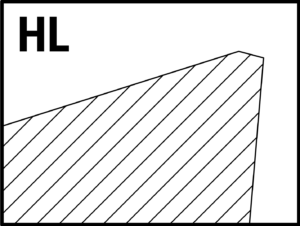
USPOT Insert Code Generator & Tool-Holder Helper
All inputs are required except Material Hardness (HRC) and Coating, which are optional.