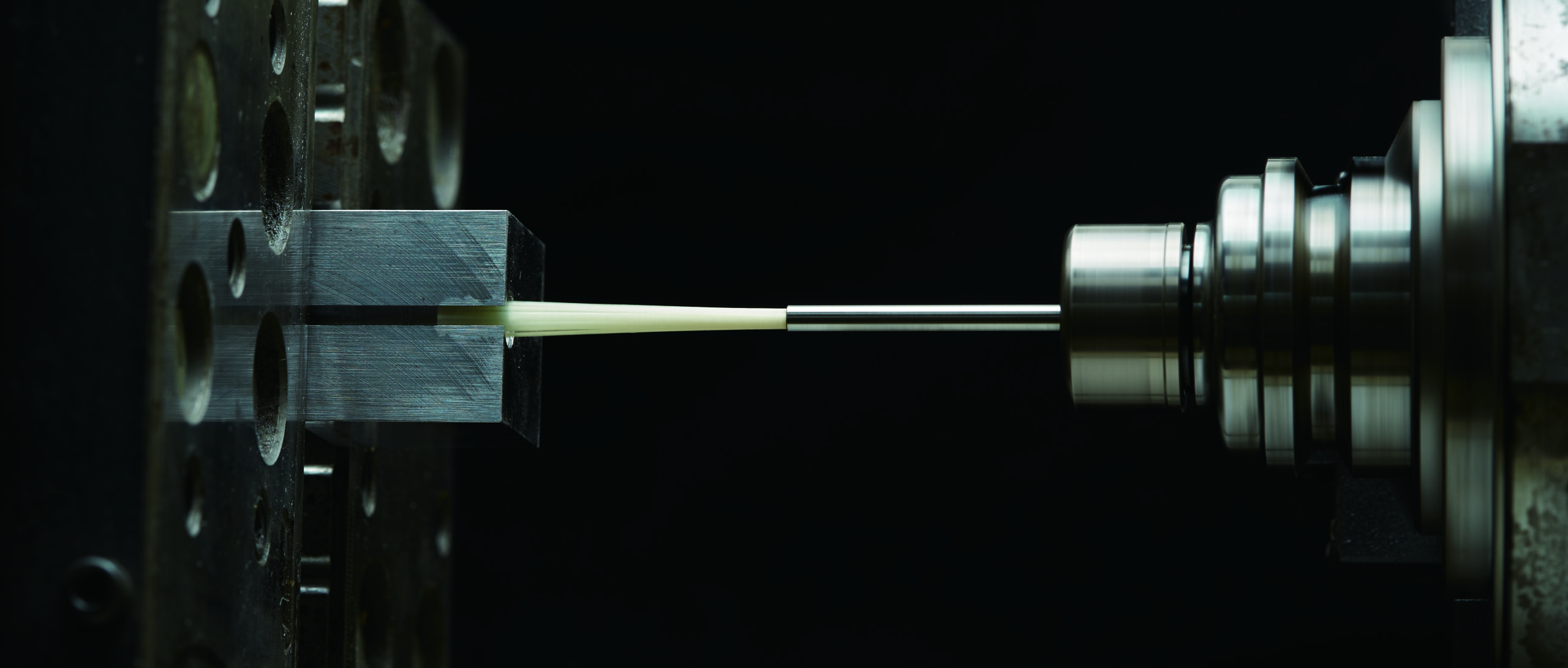
Cross-Hole Brush Machining Guidelines and Safety Instructions
Features:
- The brush expands under centrifugal force during rotation, effectively removing fine burrs from the cylinder’s inner surface.
- It helps prevent and eliminate black scale from inside the cylinder.
- Removes cutting particles and prevents burrs from adhering to surfaces.
- Made from ceramic fiber, it removes burrs using the cutting edges of the fibers.
- Suitable for removing inner surface burrs in steel, aluminium, stainless steel, composite and resin materials.
- Can be installed on machining centers, robots, or other processing equipment.
- Efficiently removes cutting, polishing, and processing residues.
Machining Recommendations:
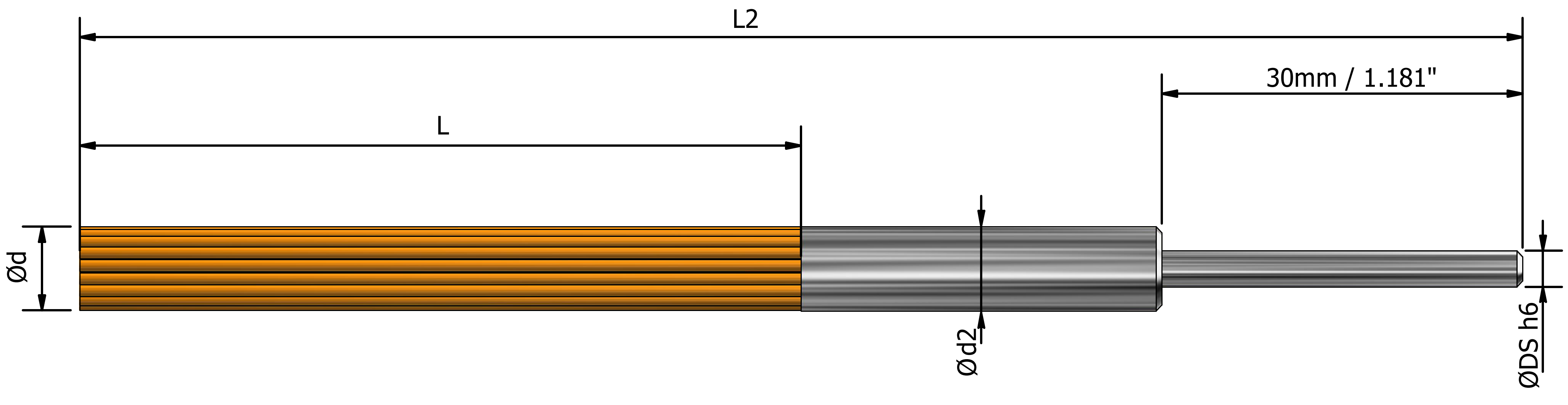
SKU# | DESCRIPTION | Grit Size | Ød mm | L mm | Ød2 mm | L2 mm | ØDS mm | Weight gram | Maximum Spindle Speed Min-1 | Suitable Pilot-hole diameter | |
Grit #150-#1000 mm | Grit #1200-#6000 mm | ||||||||||
UF2115 | UF-CH-G-D015-L50 | 150 | Ø1.5 | 50 | Ø2.5 | 120 | Ø3 | 3 | 20000 | 3.5-5 | 3.5-5 |
UF2215 | UF-CH-P-D015-L50 | 200 | |||||||||
UF2315 | UF-CH-V-D015-L50 | 400 | |||||||||
UF2415 | UF-CH-O-D015-L50 | 600 | |||||||||
UF2515 | UF-CH-B-D015-L50 | 800 | |||||||||
UF2615 | UF-CH-W-D015-L50 | 1000 | |||||||||
UF2715 | UF-CH-R-D015-L50 | 1200 | |||||||||
UF2815 | UF-CH-M-D015-L50 | 2000 | |||||||||
UF2915 | UF-CH-Z-D015-L50 | 3000 | |||||||||
UF2015 | UF-CH-A-D015-L50 | 6000 | |||||||||
UF2130 | UF-CH-G-D030-L60 | 150 | Ø3 | 60 | Ø4 | 130 | Ø3 | 6 | 14000 | 5-7 | – |
UF2230 | UF-CH-P-D030-L60 | 200 | |||||||||
UF2330 | UF-CH-V-D030-L60 | 400 | |||||||||
UF2430 | UF-CH-O-D030-L60 | 600 | |||||||||
UF2530 | UF-CH-B-D030-L60 | 800 | |||||||||
UF2630 | UF-CH-W-D030-L60 | 1000 | |||||||||
UF2730 | UF-CH-R-D030-L50 | 1200 | 50 | 120 | 14000 | – | 5-7 | ||||
UF2830 | UF-CH-M-D030-L50 | 2000 | |||||||||
UF2930 | UF-CH-Z-D030-L50 | 3000 | |||||||||
UF2030 | UF-CH-A-D030-L50 | 6000 | |||||||||
UF2150 | UF-CH-G-D050-L60 | 150 | Ø5 | 60 | Ø6 | 130 | Ø6 | 17 | 14000 | 7-9 | – |
UF2250 | UF-CH-P-D050-L60 | 200 | |||||||||
UF2350 | UF-CH-V-D050-L60 | 400 | |||||||||
UF2450 | UF-CH-O-D050-L60 | 600 | |||||||||
UF2550 | UF-CH-B-D050-L60 | 800 | |||||||||
UF2650 | UF-CH-W-D050-L60 | 1000 | |||||||||
UF2750 | UF-CH-R-D050-L50 | 1200 | 50 | 120 | 14000 | – | 8-10 | ||||
UF2850 | UF-CH-M-D050-L50 | 2000 | |||||||||
UF2950 | UF-CH-Z-D050-L50 | 3000 | |||||||||
UF2050 | UF-CH-A-D050-L50 | 6000 | |||||||||
UF2170 | UF-CH-G-D070-L60 | 150 | Ø7 | 60 | Ø8 | 130 | Ø6 | 24 | 14000 | 9-14 | – |
UF2270 | UF-CH-P-D070-L60 | 200 | |||||||||
UF2370 | UF-CH-V-D070-L60 | 400 | |||||||||
UF2470 | UF-CH-O-D070-L60 | 600 | |||||||||
UF2570 | UF-CH-B-D070-L60 | 800 | |||||||||
UF2670 | UF-CH-W-D070-L60 | 1000 | |||||||||
UF2770 | UF-CH-R-D070-L50 | 1200 | 50 | 120 | 14000 | – | 10-20 | ||||
UF2870 | UF-CH-M-D070-L50 | 2000 | |||||||||
UF2970 | UF-CH-Z-D070-L50 | 3000 | |||||||||
UF2070 | UF-CH-A-D070-L50 | 6000 |
Grit Selection by Burr Condition & Material
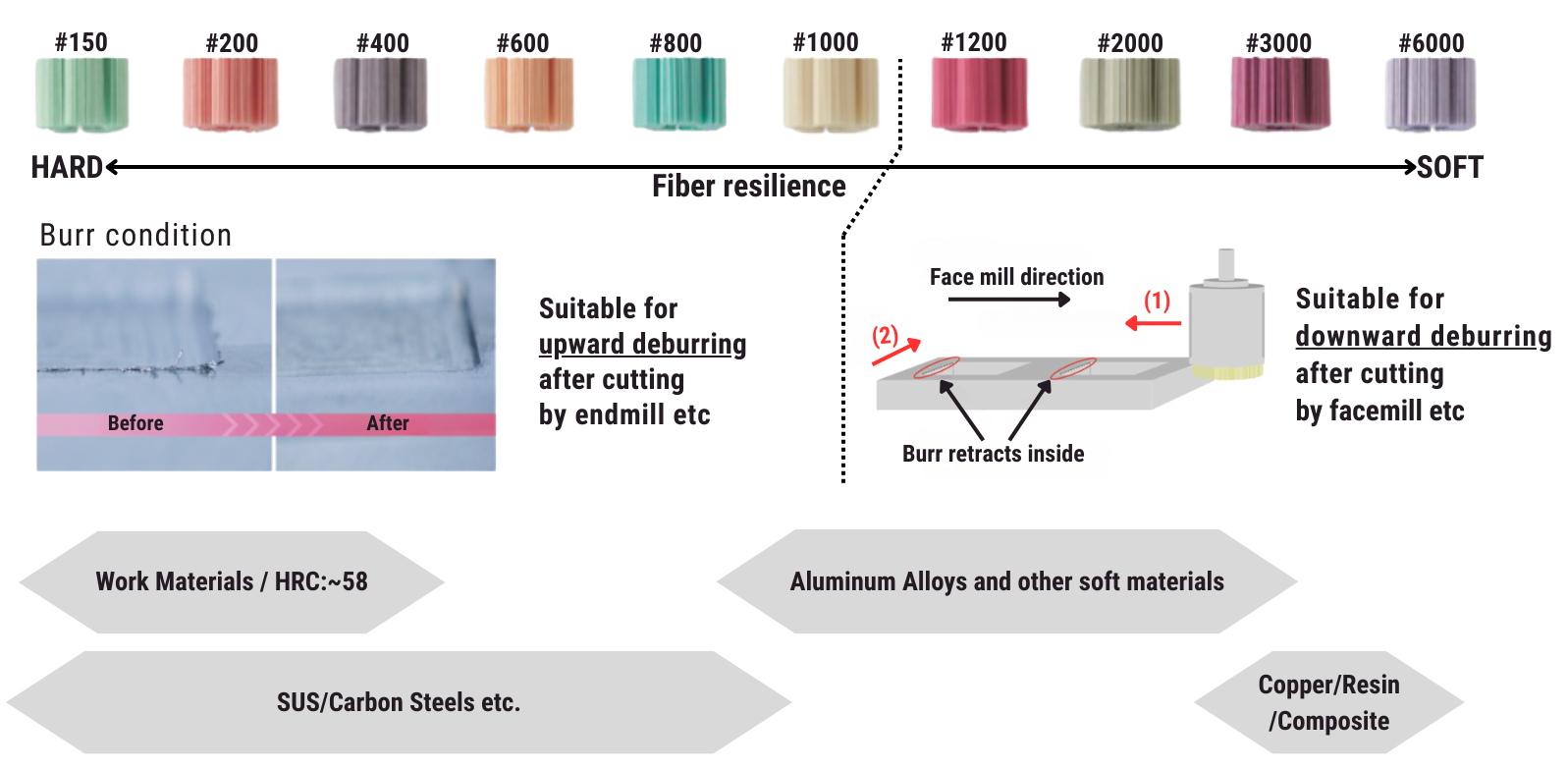
How to Use the UFIBER Cross-Holes Brushes:
- Insert the brush without rotation: Ensure the brush is stationary when inserting it into the cylinder to prevent damage to the bristles or scattering, which could lead to operator injury.
- Rotate the tool through the cross-hole: Achieve consistent edge quality by rotating the tool in both clockwise and counterclockwise directions.
- Pull the brush back while processing: Retracting the brush through the cross-holes prevents burrs from being pressed flat against the cylinder’s inner surface.
- Push the brush forward during processing: Advancing the brush forward helps in removing any upward-facing burrs that remain.
- Stop the brush rotation
- Change rotation direction
- Repeat steps 3,4,5
- Remove the brush while stationary: Ensure the brush is completely stopped before removal.
Cross-Hole Brush Diameter Control Guidelines:
This section provides guidance on how to manage and optimize the outer diameter of brushes across different grit levels by adjusting the rotational speed (RPM). Understanding this relationship is crucial for achieving the desired surface finish during polishing and deburring processes.
Understanding the Relationship Between RPM and Brush Diameter:
Rotational Speed (RPM): As the speed of the brush rotation increases, the brush fibers spread outward due to centrifugal force. This results in an increase in the brush’s outer diameter.
Grit Levels: Brushes come in different grit levels, which determine their coarseness. Coarser grits (e.g., #400) tend to have less variation in diameter with increasing RPM, whereas finer grits (e.g., #1000 and above) show a more pronounced increase in diameter.
Using the cross-hole with different shaped holes:
1.For T-shaped Holes:
where the diameter of the cross hole (dcross) must be less than the diameter of the main bore (dmain).
dcross < dmain
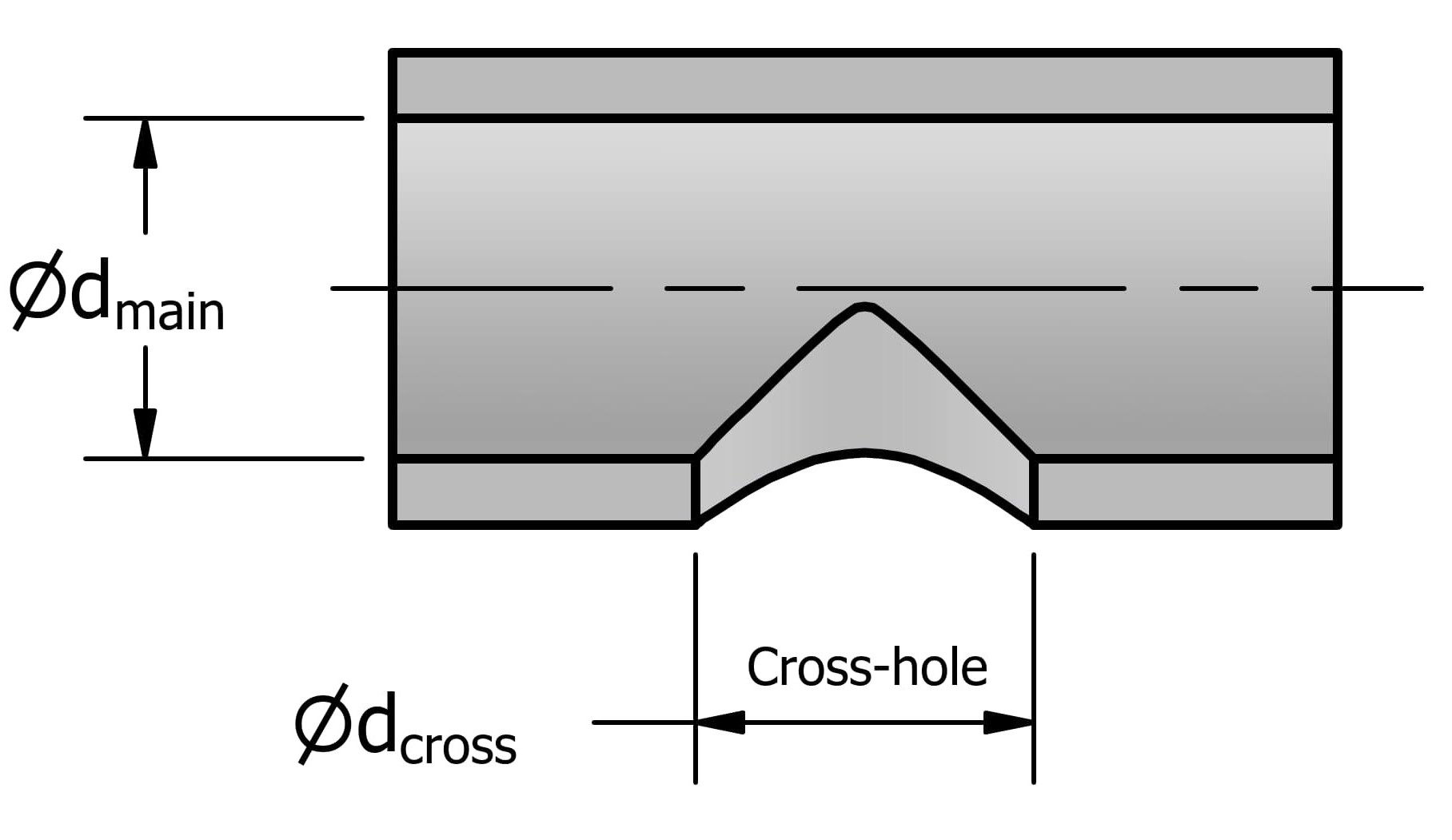
2.For Cross-shaped Holes where the diameter of the cross hole d(cross) must be 70% or less of the diameter of the main bore (dmain) .
dcross<0.7*dmain
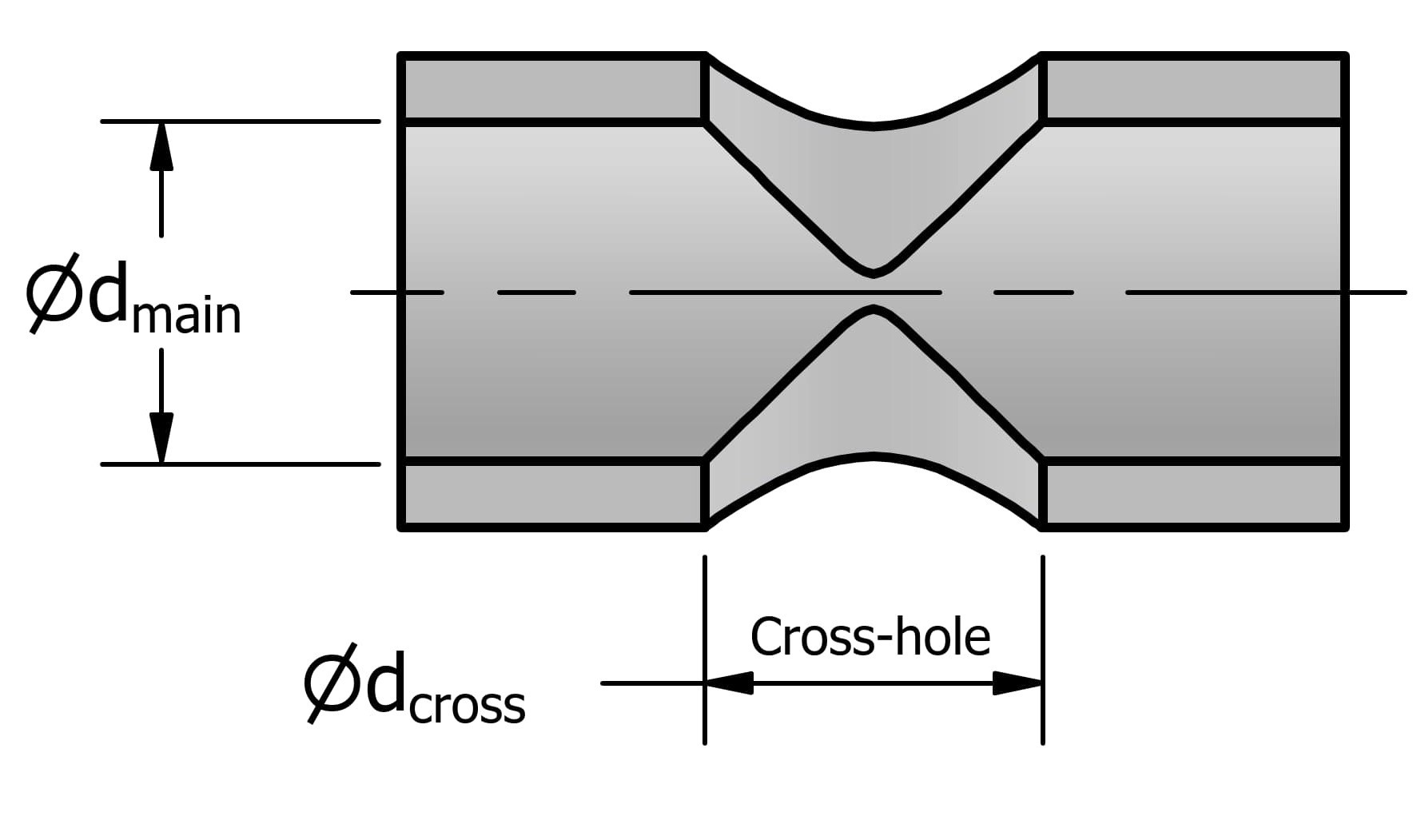
Cross-Hole Safety Precautions:
- Ensure that the tool operates within the recommended maximum rotational speed to prevent brush damage.
- The tool should be used within the cylinder or workpiece area to avoid unnecessary wear on the brush.
- It is suitable for processing centered holes and cross holes that are properly aligned.
- When installing the tool, ensure that the shank is gripped by at least 30mm. Failure to do so may cause the tool to detach due to vibrations, posing a risk of serious injury, including loss of sight.
- Use a chuck that matches the shank diameter, and ensure the processing equipment can control the rotational speed.
Cross-Hole Safety Instructions:
Please adhere strictly to the instructions provided in this guide. Using the product in a manner not specified here may result in serious injury or even fatality.
CAUTION:
The use of this product carries a risk of serious injury, including eye injury or blindness, if the product detaches from the equipment, if bristles break off, or if workpieces fracture. Particles such as fragments, debris, and burrs generated during processing can penetrate the eyes or skin, leading to serious harm. Dust from the process can damage lungs, irritate the skin, and cause allergic reactions.
If you detect any vibration or other unusual occurrences during use, stop immediately. Continuing to use the product under such conditions increases the risk of it detaching, breaking off bristles, or causing workpieces to break, potentially leading to severe injury.
Exceeding the recommended rotational speed can also cause detachment, bristle breakage, or workpiece fractures, posing serious risks to the operator. Extended machining at a constant point can cause the tool tip to overheat, increasing the likelihood of bristle detachment or breakage. To avoid this, adjust processing times to prevent overheating, and avoid direct contact with the machined area with bare hands after use.
NOTE:
The situations described above also pose risks of damage to machining tools, jigs, and workpieces.
Operator Safety Measures:
Protective Gear: Always wear appropriate personal protective equipment, including safety goggles, masks, gloves, and hearing protection, to minimize injury risks during machining. Wear long-sleeved clothing that fully covers the skin, and secure cuffs and hems tightly.
Work Area Safety: Install barriers to prevent unauthorized personnel from entering the work area, and ensure that anyone present is wearing protective equipment. Take special care to keep children out of the work area. Keep the floor clean and free of debris, cutting particles, oil, water, and other substances to prevent slips or falls.
Fire Safety: This product can generate heat or sparks, potentially causing fires. Do not use it near flammable liquids or in explosive atmospheres. Implement appropriate fire prevention measures.
Handling Cutting Particles:
Processing with this product generates fragments and debris that may scatter. Use a dust collection system or similar method to capture these particles.
Usage Guidelines:
- When installing the tool, ensure that the shank is gripped by at least 30mm. Failure to do so may cause the tool to detach due to vibrations, posing a risk of serious injury, including loss of sight.
- Use a chuck that matches the shank diameter, and ensure the processing equipment can control the rotational speed.