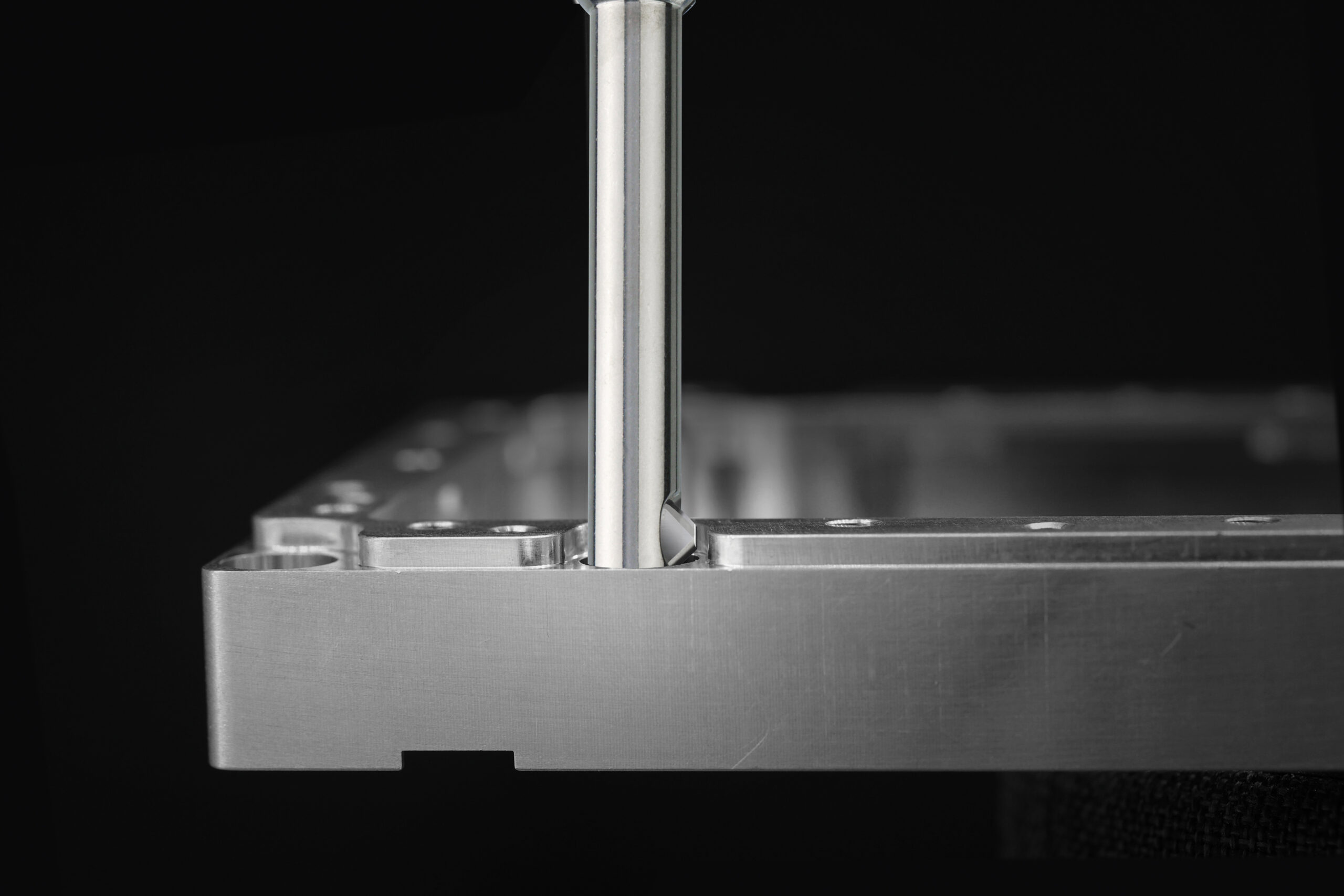
Case Studies
UBURR CASE STUDY #1
Case Study #1 UBURR Industry: Automotive Objective: Conduct comparison tests against competitors for removing burrs from the front and rear of machined drills. Application details: Part: Transmission Shaft Material: AISI 4340, Wr N.1.6928 Pilot Holes: Ø2.5 and Ø3.0mm / .098
UBURR CASE STUDY #2
Case Study #2 UBURR Industry: Cutting Tools Manufacture Goal: Removing burrs from rearmachined drills made for clamping screw Application details: Material: AISI 4340, Wr N.1.6928 with 45HRc hardness Pilot Holes: Ø5mm / .197” Pilot Hole Length: H1=50mm / 1.97” Machine:
UBURR CASE STUDY #3
Case Study #3 UBURR Industry: Medical Objective: Remove burrs from the front and rear of machined drills for Arthroscopy scissors. The Arthroscopy scissor Joint is a reusable system that integrates advanced quality, durability, and precise tactility in each instrument to
UBURR CASE STUDY #4
Case Study #4 UBURR Industry: General Objective: Test the UBURR tools on hardened materials and eliminate burrs from the front and rear of machined drills. Application details: Material: AISI H13, Wr N.1.2344 pallets with 60HRc hardness Pilot Holes: Ø7mm /
UBURR CASE STUDY #5
Case Study #5 UBURR Industry: General Objective: Evaluate the UBURR tools on machined threads and eliminate burrs from both the front and rear of machined drills. Application details: Material: AISI 4340, Wr N.1.6928 Tool Steel with 38HRc hardness Pilot Holes: