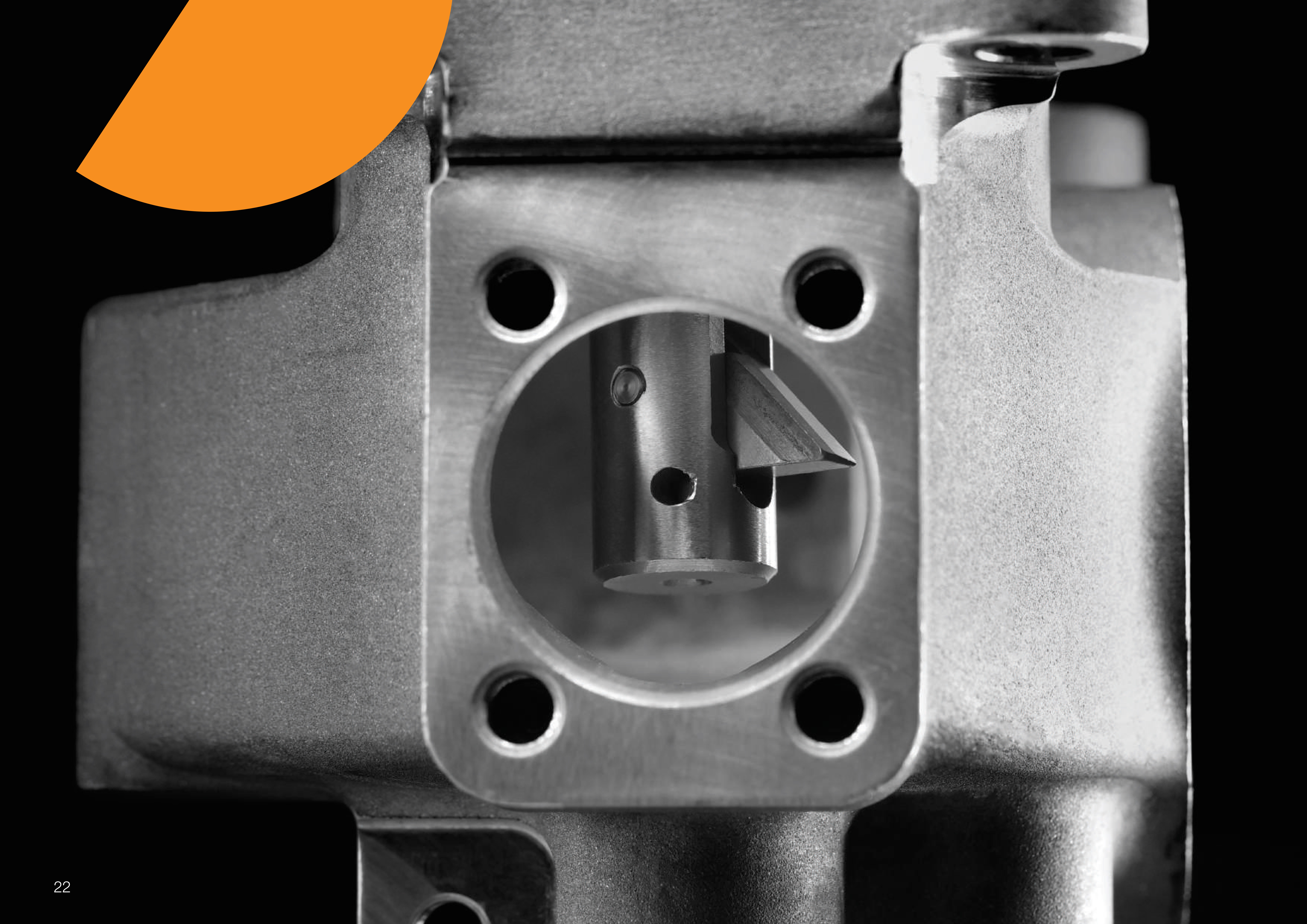
UBACK Technical Guidelines
- How does the UBackTool works?
- UBack Programming guidelines
- UBack Insert Replacement
- Counterbore Machining Guidelines for Specific Conditions
- Configuring UBACK tool-holders for different cooling systems
- UBack cutting recommendations
- Coatings Types
- Chip-formers
- NEW UBACK-USPOT Insert and Tool-Holder Configurator
- NEW UBACK-UCHAMF Insert and Tool-Holder Configurator
How does the UBackTool works?
- The UBack tool-holders are designed for CNC automated operations and are compatible with USPOT inserts for back counterboring and spot-facing, as well as UCHAMF inserts for back countersinking.
- The insert’s opening and closing hydraulic mechanism is activated by directing coolant through the spindle and tool-holder. This system supports coolant, emulsion, or air with a minimum pump pressure of 6 bar (90 PSI).
- The tool-holder is specifically engineered to prevent scratches while passing through the pilot hole.
(1) The Folding Length (FL) parameter is listed in the tool-holder tables and is the same for both USPOT inserts and UCHAMF inserts.
(2) The illustrated operation sequence above demonstrates working with a USPOT insert but remains the same when using a UCHAMF insert.
UBack Tool Insert Replacement
- UBack inserts can be easily replaced using just a pin and a screw, without the need for any additional mounting devices.
- The pin is used to secure the insert within the tool-holder, preventing it from retracting while unscrewing.
- The UBack spare parts, including the screw, key, and pin, are standardized across the entire UBack tool-holder range.
NOTE: The illustrated insert replacement above is demonstrated with a USPOT insert but remains the same when using a UCHAMF insert.
Counterbore Machining Guidelines for Specific Conditions
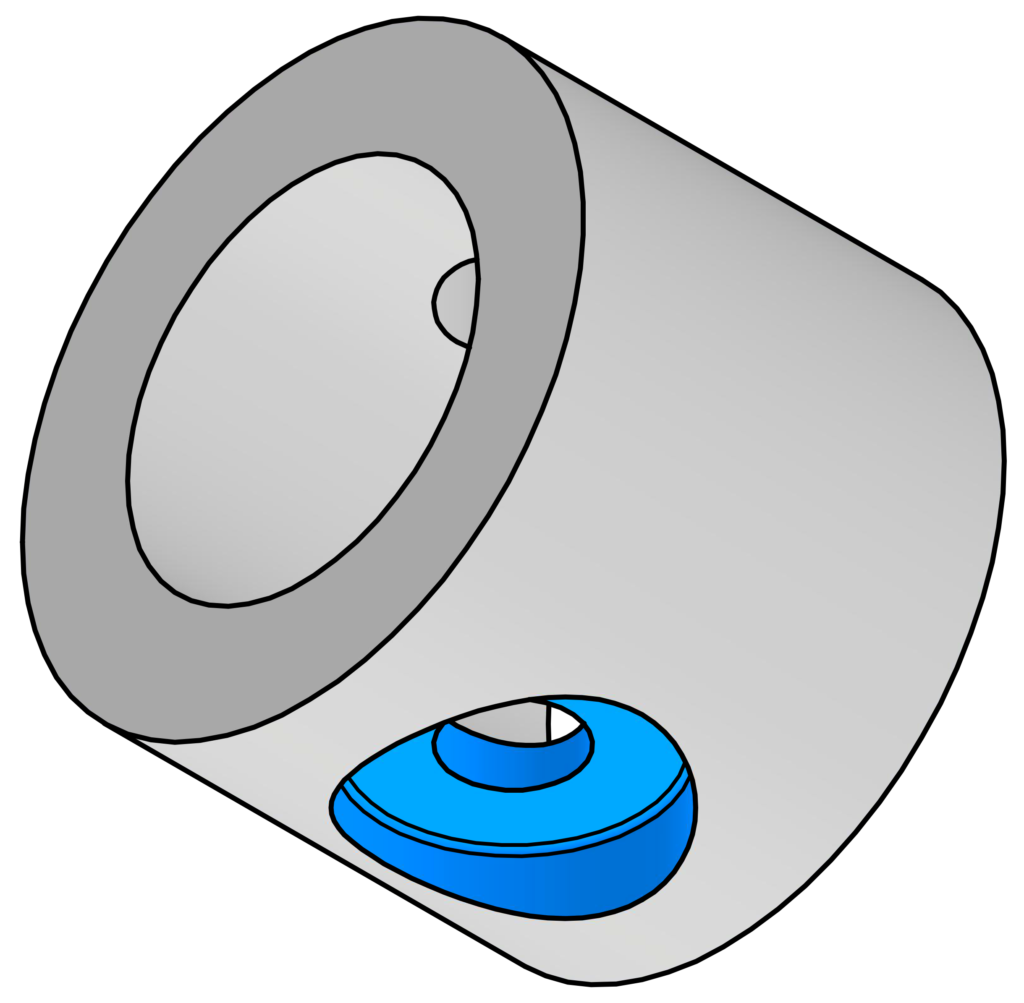
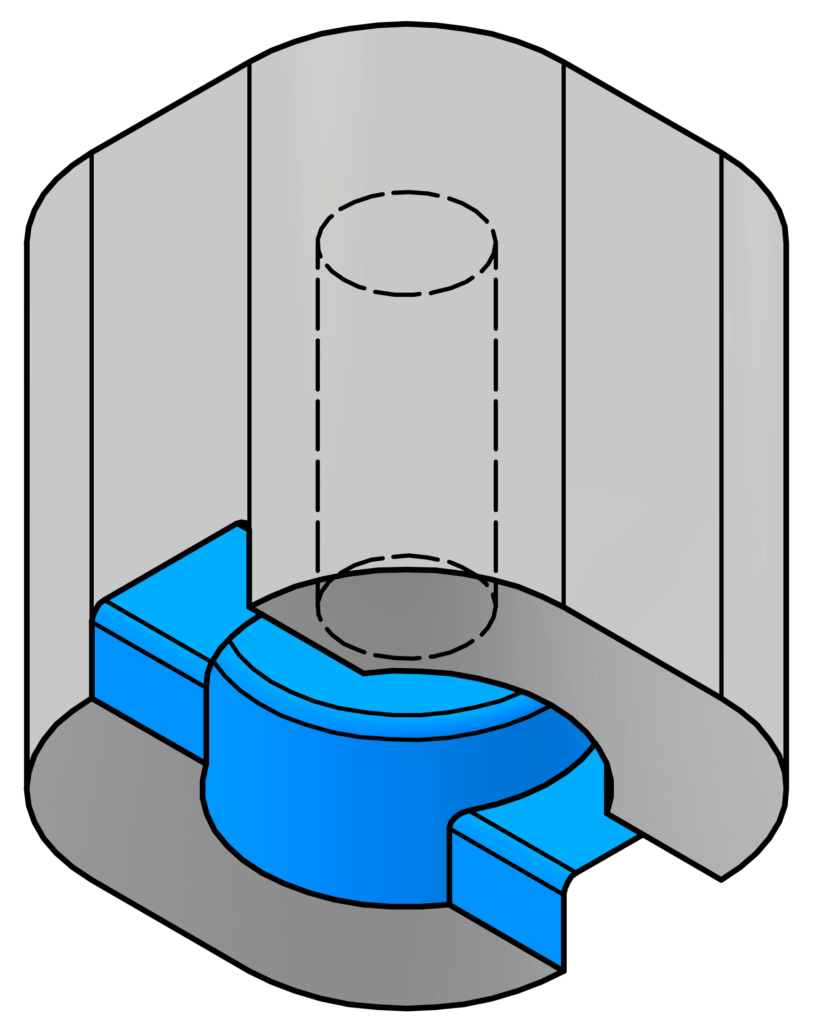
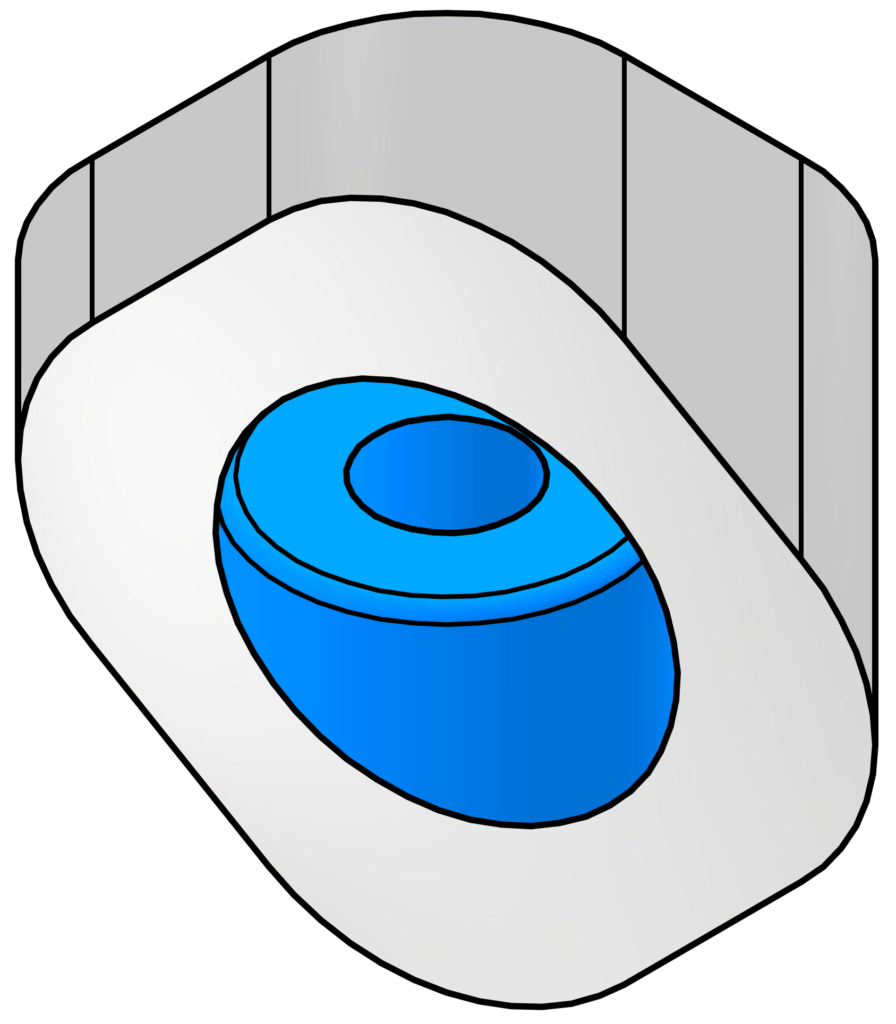
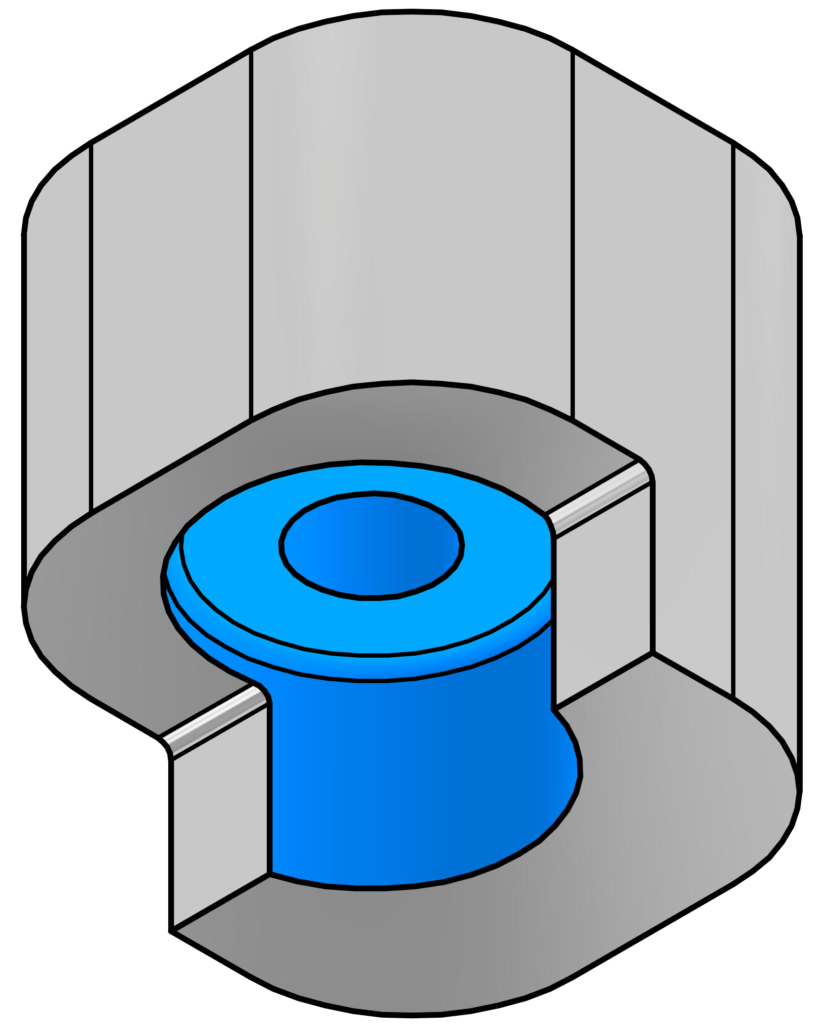

Counterbore on Cylindrical Bore
- Use with Internal Coolant
Counterbore on Sloped Surface
- Use external coolant only
- Fully Interrupted Cut
- Use external coolant only
- Consider reduced stability and adjust cutting parameters by reducing them by 30%
- Fully Interrupted Cut
- Use external coolant only
- Consider reduced stability and adjust cutting parameters by reducing them by 30%
- Fully Interrupted Cut
- Use external coolant only
- Consider reduced stability and adjust cutting parameters by reducing them by 30%
Configuring UBACK tool-holders for different cooling systems
UBack Cutting Recommendations
The table below presents cutting recommendations, outlining initial feed rates and cutting speed for materials group based on ISO 513 and VDI 3323 standards.
(1) To ensure optimal performance and tool-life under varying conditions:
- For moderate tool-holder or workpiece stability, consider reducing feed rates by up to 10%.
- For poor tool-holder or workpiece stability, it’s advisable to decrease feed rates by up to 30%.
Additionally, the operator must ensure the utilization of appropriate coolant media directed to the cutting tip of the blade and right-hand machining (clockwise).
ISO |
Material |
Condition |
As is |
DIN W.-Nr. |
vc(1) cutting speed |
Series B |
Series C |
Series D |
Series E |
Series F |
Series G |
Recommended |
Coolant |
|
|||
P |
Non-alloy steel |
<0.25% C |
Annealed |
1020 |
1.0044 |
60-120 |
0.03 |
0.04 |
0.05 |
0.07 |
0.08 |
0.09 |
PL ML |
Air / Wet |
|||
≥0.25% C |
Annealed |
1035 |
1.0501 |
||||||||||||||
<0.55% C |
Quenched and tempered |
1045 |
1.1201 |
||||||||||||||
≥0.55% C |
Annealed |
1055 |
1.0535 |
||||||||||||||
Quenched and tempered |
1060 |
1.1221 |
|||||||||||||||
Low alloy |
Annealed |
G92600 |
1.5028 |
50-120 |
0.03 |
0.04 |
0.05 |
0.07 |
0.08 |
0.09 |
|||||||
Quenched and tempered |
4130 |
1.7218 |
|||||||||||||||
4142 |
1.2332 |
||||||||||||||||
5045 |
1.7006 |
50-100 |
|||||||||||||||
High alloyed steel, |
Annealed |
H13 |
1.2344 |
40-90 |
0.02 |
0.03 |
0.04 |
0.05 |
0.06 |
0.08 |
|||||||
Quenched and tempered |
M33 |
1.3249 |
|||||||||||||||
Stainless steel and cast
steel |
Ferritic/martensitic |
420 |
1.4021 |
||||||||||||||
Martensitic |
|||||||||||||||||
M |
Stainless steel |
Austenitic, duplex |
304L |
1.4306 |
50-100 |
0.03 |
0.04 |
0.05 |
0.07 |
0.08 |
0.09 |
PL |
Wet |
||||
K |
Gray cast iron (GG) |
Ferritic / pearlitic |
Class 25 |
0.6015 |
60-120 |
0.03 |
0.04 |
0.05 |
0.07 |
0.08 |
0.09 |
PL |
Air / Wet |
||||
Pearlitic / martensitic |
Grade H20 |
36037 |
|||||||||||||||
Nodular cast iron (GGG) |
Ferritic |
60-40-18 |
0.7043 |
50-100 |
0.02 |
0.03 |
0.04 |
0.05 |
0.06 |
0.08 |
|||||||
Pearlitic |
F33500 |
0.705 |
|||||||||||||||
Malleable cast iron |
Ferritic |
A47 |
0.8135 |
||||||||||||||
Pearlitic |
A220 Class |
0.8155 |
|||||||||||||||
N |
Aluminum-wrought alloys |
Not hardenable |
5005 |
3.3315 |
100-160 |
0.05 |
0.06 |
0.08 |
0.10 |
0.12 |
0.14 |
PL |
Wet |
||||
Hardenable |
7075 |
3.4365 |
|||||||||||||||
Aluminum-cast alloys |
≤12% Si |
Not hardenable |
518 |
3.3292 |
|||||||||||||
Hardenable |
515 |
3.3241 |
|||||||||||||||
>12% Si |
High temperature |
390 |
|
||||||||||||||
Copper alloys |
>1% Pb |
Free cutting |
C36000 |
2.0375 |
90-130 |
||||||||||||
|
Brass |
C22000 |
2.023 |
||||||||||||||
Electrolytic copper |
C63000 |
2.0966 |
|||||||||||||||
Non metallic |
Duroplastics, fiber
plastics |
Bakelite |
|
180-305 |
|||||||||||||
Hard rubber |
Ebonite |
|
|||||||||||||||
S |
High temperature alloys |
Fe based |
Annealed |
330 |
1.4864 |
40-80 |
0.02 |
0.03 |
0.04 |
0.05 |
0.06 |
0.08 |
PL ML |
Wet |
|||
Hardened |
S590 |
1.4977 |
|||||||||||||||
Ni or Co based |
Annealed |
Incoloy 825 |
2.4858 |
25-40 |
|||||||||||||
Hardened |
Inconel 718 |
2.4668 |
|||||||||||||||
Cast |
Nimocast K24 |
2.4674 |
|||||||||||||||
Titanium alloys |
Pure |
Titanium G.1 |
3.7024 |
30-60 |
0.02 |
0.03 |
0.04 |
0.05 |
0.06 |
0.08 |
|||||||
Alpha+beta alloys,
hardened |
Titanium G.5 |
3.7165 |
|||||||||||||||
H |
Hardened steel |
Hardened |
HARDOX 500 |
|
30-50 |
0.02 |
0.02 |
0.03 |
0.04 |
0.05 |
0.06 |
ML HL |
Air |
||||
Hardened |
HARDOX Extreme |
|
30-40 |
||||||||||||||
Chilled cast iron |
Cast |
A532 lllA 25% Cr |
0.965 |
45-50 |
0.02 |
0.02 |
0.03 |
0.04 |
0.05 |
0.06 |
|||||||
Cast iron |
Hardened |
A532 IID 20% CrMo |
0.9645 |
30-50 |
0.02 |
0.02 |
0.03 |
0.04 |
0.05 |
0.06 |
|||||||
(1) To ensure optimal performance and tool-life under varying conditions:
- For moderate tool-holder or workpiece stability, consider reducing feed rates by up to 10%.
- For poor tool-holder or workpiece stability, it’s advisable to decrease feed rates by up to 30%.
Available Coating types and surface treatments:
Coating |
Key Features |
Applications |
Industries |
Material Examples |
ISO GROUP |
|||||
P |
M |
K |
N |
S |
H |
|||||
TiAlN |
Suitable for mid steels, cast iron, stainless steel, titanium alloys, Inconel, tool steel, and hardened steels. Offers excellent thermal stability, oxidation resistance, and wear resistance. |
Ideal for high-speed cutting and general-purpose machining. Performs well in both wet and dry conditions. |
Aerospace, Automotive, General Engineering |
AISI 304, 42CrMo4, GG (Grey Cast Iron), Ti6Al4V |
✓ |
✓ |
✓ |
X |
✓ |
✓ |
TiAlSiN |
Provides exceptional hardness and oxidation resis9tance, withstanding temperatures above 1,200°C. Suitable for high-strength steels, superalloys, hardened steels (over 45 Rc), and titanium alloys. |
Best for high-performance machining in demanding environments. Excels in dry machining at high speeds. |
Aerospace, Automotive, Die and Mold |
Inconel 718, AISI 4140, Ti6Al4V |
✓ |
✓ |
X |
X |
✓ |
X |
AlTiSiN |
Offers high hardness, thermal stability, and resistance to wear and oxidation. Suitable for stainless steel, hardened cast, superalloys, and steels over 45 Rc. |
Designed for high-speed machining in extreme conditions. Performs exceptionally in dry machining. |
Aerospace, Automotive, Precision Engineering |
AISI 316, AISI H13, Hastelloy |
X |
✓ |
X |
X |
✓ |
✓ |
AlCrN |
Provides excellent oxidation resistance (up to 1,100°C), toughness, and abrasion resistance. Suitable for carbon steels, cast iron, stainless steel, and aluminum. |
Suitable for general machining in wet and dry environments. Excels in abrasive and high-wear applications. |
Automotive, Aerospace, Die and Mold |
AISI 304, AISI 1045, GG, AL6061 |
✓ |
X |
✓ |
✓ |
X |
X |
AlTiN |
High hardness, wear resistance, and thermal stability up to 1,100°C. Designed for mid steels, cast iron, high-speed steels, tool steel, and hardened materials. |
Ideal for heavy-duty machining and high-speed cutting. Performs well in dry and abrasive conditions. |
Aerospace, Automotive, Heavy Engineering |
AISI 4340, M2 HSS, GG (Grey Cast Iron) |
✓ |
✓ |
✓ |
X |
X |
X |
TiB2 |
Kknown for exceptional chemical stability, low friction, and high thermal conductivity. Best for machining non-ferrous materials such as aluminium, copper, brass, and magnesium alloys. Reduces friction and Built-Up Edge. (BUE) |
Optimized for high-speed machining of non-ferrous metals. Prevents material adhesion and improves efficiency. |
Aerospace, Automotive, Electronics |
AL7075, 6061-T6, Copper, Magnesium Alloys (AZ31) |
X |
X |
X |
✓ |
✓ |
X |
Polishing |
Provides a smooth, refined surface finish by removing micro-defects, scratches, or burrs. Enhances aesthetics and surface quality. Reduces friction and BUE. |
Suitable for machining aluminium with high speeds and high MRR (Metal Removal Rates) |
Aerospace, Automotive |
AL7075, 6061-T6, Copper, Magnesium Alloys (AZ31) |
X |
X |
X |
✓ |
X |
X |
Chip-formers:
PL
Positive cutting land
Suitable for all around purpose
and ISO P,M,K,N,S
as well as composite materials
ML
Moderate cutting land
Suitable for and ISO P,M,K,S,H
Materials
HL
Negative cutting land
Suitable for and ISO P,M,K,S,H
Materials
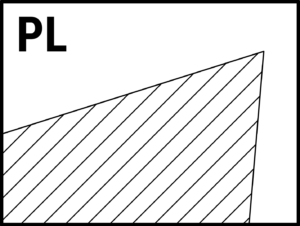
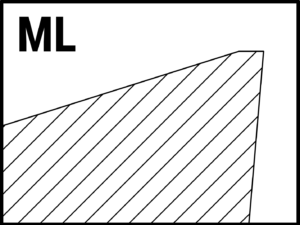
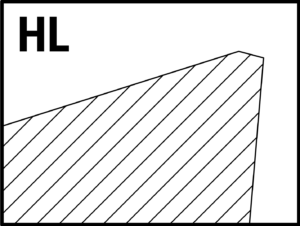
Try Using Our USPOT Insert Code Generator
& Tool-Holder Configurator
All fields are required except Material Hardness (HRC) and Coating
Default corner radius: 0.4
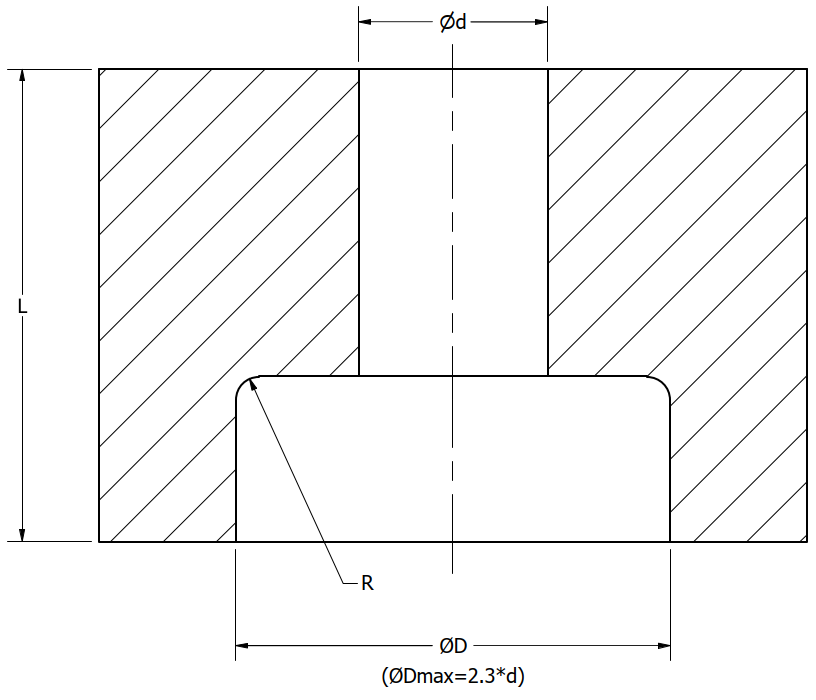
Try Using Our UCHAMF Insert Code Generator
& Tool-Holder Configurator
All inputs are required except Material Hardness (HRC) and Coating.
Default Countersink Angle: 90° (Metric), 82° (Imperial)
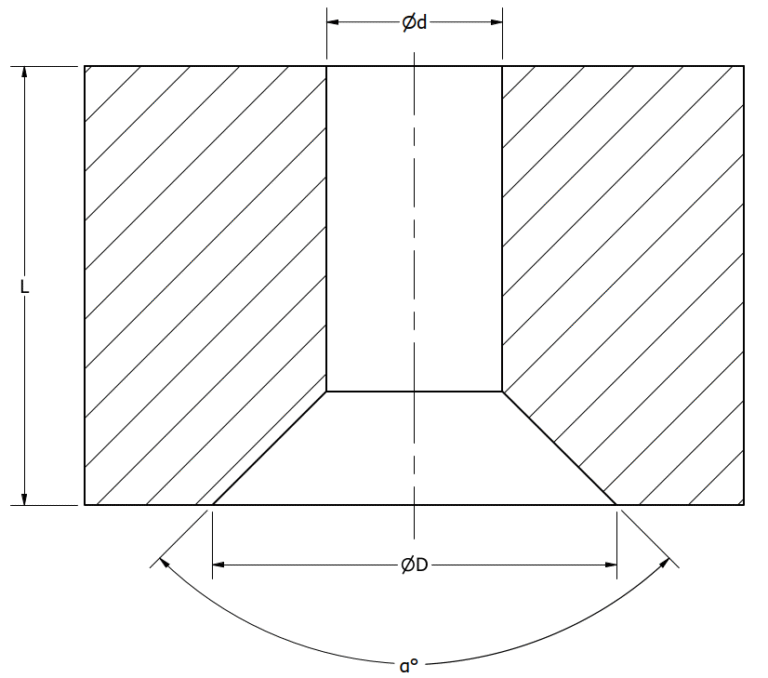